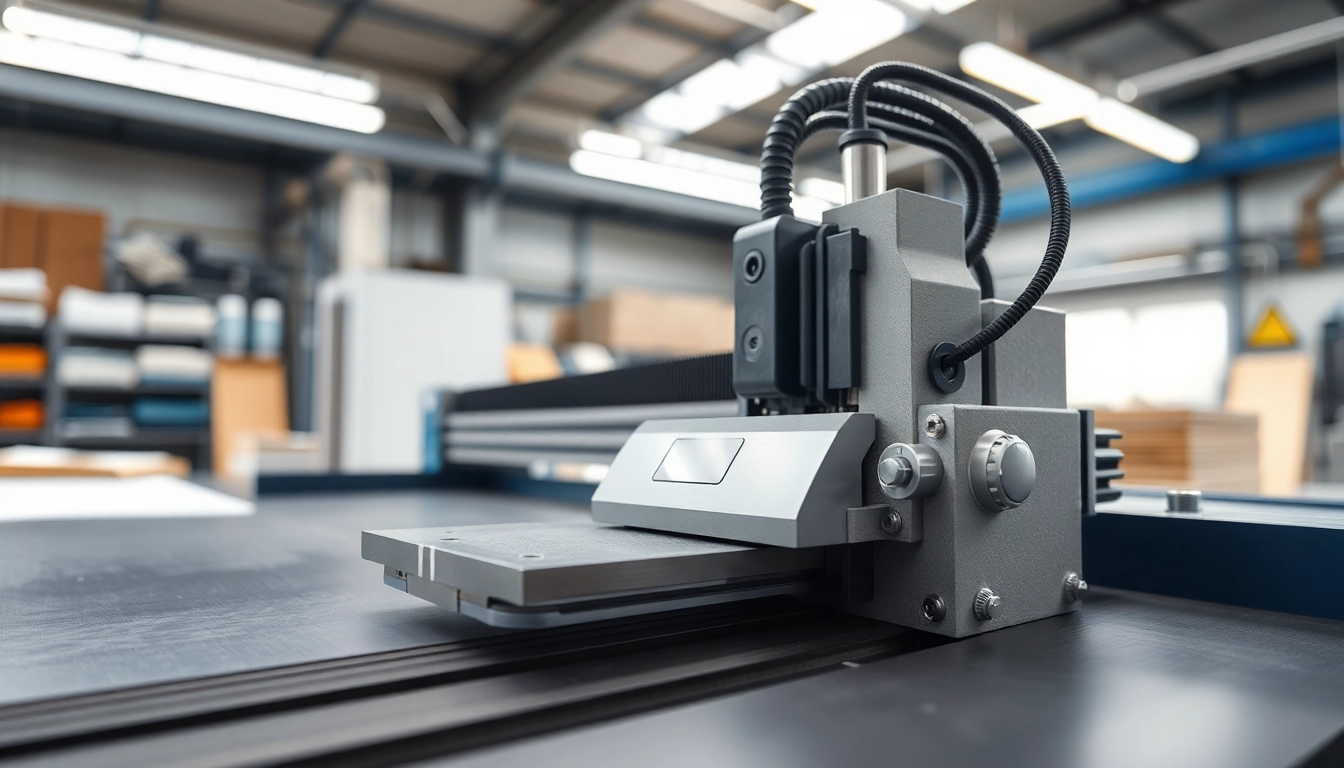
Understanding Precision Die Cutting
Definition and Overview of Precision Die Cutting
Precision die cutting is an advanced manufacturing process used to create custom shapes from various materials with high accuracy and efficiency. Unlike traditional cutting methods, precision die cutting utilizes a die, or custom-made blade, to cut sheets or rolls of material into the desired form. This method ensures clean edges, intricate designs, and uniformity, essential for applications in sectors like packaging, automotive, electronics, and medical manufacturing.
The precision of this method can significantly enhance product quality, reduce production time and waste, and create opportunities for complex designs that would be challenging or impossible with other cutting techniques. For those looking to explore the intricacies of this process, precision die cutting serves as an effective option to meet diverse manufacturing needs.
The Importance of Precision in Manufacturing
Precision in manufacturing is critical, especially when it comes to creating components that fit together seamlessly or when producing large quantities of items that require consistency. In industries such as electronics, even the slightest variation can lead to product failure. Precision die cutting minimizes such risks by providing measurements that are exact, ensuring that each part produced matches the specifications and standards required by the design.
Moreover, the rise of automation in manufacturing means that precision die cutting methods can integrate smoothly into production lines, increasing overall efficiency. The ability to maintain tight tolerances means that manufacturers can achieve the scalability needed for mass production without sacrificing quality.
Common Applications Across Industries
Precision die cutting finds applications in numerous industries, including:
- Packaging: Custom packaging solutions often require intricately designed cartons and inserts that die cutting can produce with ease.
- Electronics: Components such as seals, gaskets, and insulation require precise cuts to ensure fit and function.
- Medical: Surgical instruments and medical device components often rely on precision die cutting for accuracy and compliance with regulations.
- Automotive: Parts such as insulation and sealing materials need to be cut to exact specifications to perform their functions effectively.
- Textiles: From fashion to upholstery, die cutting can create patterns and shapes that are complex and tailored to fit design needs.
Types of Precision Die Cutting Techniques
Rotary Die Cutting: Advantages and Disadvantages
Rotary die cutting involves a rotatable drum equipped with sharp blades that cut materials as they pass through. This method is highly efficient, particularly for high-volume production runs. The continuous feed allows for fast processing, making it ideal for items that require repetitive cuts like labels or promotional materials.
However, rotary die cutting has its drawbacks. The initial set-up cost can be high due to the need for custom dies, which makes it less economically viable for small production runs. Additionally, this method can be limited to specific material gauges, which may not suit every application.
Flatbed Die Cutting: When to Use It
Flatbed die cutting utilizes a flat surface for cutting materials, making it versatile for various shapes and sizes. This technique is beneficial for lower volume production or projects requiring complex designs. Because the cutting process is done in one layer, it’s suitable for thicker materials and can handle a wide range of substrates from paper to plastics.
Flatbed die cutting is often slower than rotary methods but is favored for its flexibility and ability to produce intricate shapes without the need for extensive setup. For businesses looking to produce custom, high-quality products in smaller batches, flatbed die cutting is a practical choice.
Digital Die Cutting: Emerging Trends and Innovations
Digital die cutting represents the frontier of cutting technology, allowing users to create cuts directly from digital files. This method eliminates the need for physical dies, enabling immediate changes and adaptations to designs without additional costs. With precise control and accuracy, digital die cutting is perfect for prototyping, short runs, and one-off projects.
Emerging trends in digital die cutting include integration with computer-aided design (CAD) software, increased capability to handle advanced materials, and the proliferation of compact, desktop machines tailored for small businesses and hobbyists. This flexibility allows for rapid iteration and customization that meets specific customer requirements.
Materials Used in Precision Die Cutting
Common Materials Suitable for Die Cutting
Precision die cutting can work with a wide range of materials, including:
- Paper and Cardstock: Ideal for promotional materials, packaging, and crafts. Easy to cut and available in numerous finishes.
- Foam: Often used for insulation, cushioning, and gaskets in various applications.
- Plastics: Types such as PVC, acrylic, and polypropylene are frequently die-cut for packaging, electronics, and consumer goods.
- Metals: Thin sheets of metals can also be die-cut using the right techniques for parts like brackets, clips, and other components.
- Textiles: Fabrics are also suitable for die cutting, particularly in the fashion and upholstery industries.
Choosing the Right Material for Your Project
Selecting the right material for precision die cutting hinges on various factors, including the final product’s application, required durability, and project budget. Material thickness and density are also critical considerations, as they influence the type of die cutting technique to utilize. Furthermore, properties such as adhesion, flexibility, and environmental resistance should be evaluated while making material choices. Consulting with a die cutting specialist can streamline this decision-making process, ensuring optimal results.
Testing and Quality Assurance of Materials
Quality assurance in material selection is paramount to the success of any die-cutting project. Testing should encompass a variety of factors:
- Compatibility: Ensure that the chosen materials can be effectively die-cut without compromising quality.
- Durability: Conduct tests to assess how well the material holds up during manufacturing and its end use.
- Adhesion: For layered products, evaluate how well materials bond under different conditions, including temperature and humidity.
- Performance Metrics: Implement psychometric or mechanical tests to measure durability, flexibility, and other relevant properties.
Benefits of Precision Die Cutting
Cost Efficiency Compared to Traditional Methods
Cost efficiency is one of the significant advantages of precision die cutting over traditional methods. While the upfront investment in dies and setup can be significant, the long-term savings gained through reduced waste, faster production times, and improved accuracy often compensate for these costs. The ability to produce high volumes without compromising quality decreases the overall unit cost, making large orders more economical.
Additionally, the reduced need for manual labor due to automation in precision die cutting further enhances cost savings. Companies can allocate resources more efficiently and focus on core operations, ultimately increasing profitability.
Speed and Scalability in Production
The speed of precision die cutting allows manufacturers to scale their operations rapidly. Techniques such as rotary cutting can process thousands of pieces per hour, making it an excellent choice for high-demand products. As businesses grow, they can easily adjust production processes to accommodate larger orders or increased complexity in designs. This scalability means that companies can respond swiftly to market demands, ensuring they remain competitive.
Customization Options for Various Industries
Customization is a hallmark benefit of precision die cutting. The technique allows for creating a wide array of designs, shapes, and sizes tailored to specific industry needs. Whether it’s intricate patterns for packaging, specialized components for electronics, or custom parts for the automotive sector, precision die cutting provides unmatched flexibility in design. This ability to tailor production keeps manufacturers ahead of trends and responsive to unique customer specifications.
Choosing the Right Precision Die Cutting Service
Evaluating Providers and Their Capabilities
When selecting a precision die cutting service, it’s crucial to evaluate potential providers based on their capabilities, experience, and quality assurance practices. Key indicators include:
- Industry Experience: Look for providers with a proven track record in your specific industry.
- Technology Utilization: Evaluate the technology and methods they employ for die cutting to ensure they are current and effective.
- Quality Certifications: Confirm that the service adheres to industry standards and holds relevant certifications for quality.
Key Questions to Ask When Working with a Supplier
Before committing to a precision die cutting supplier, consider asking questions such as:
- What types of materials are you experienced in working with?
- Can you provide samples from previous projects?
- What quality assurance processes do you have in place?
- What is your turnaround time for projects of various sizes?
- How do you handle modifications to designs once production has started?
Success Stories: Companies Excelling in Precision Die Cutting
Numerous companies have successfully leveraged precision die cutting to enhance their production capabilities. For instance, a leading packaging firm implemented precision die cutting technology to streamline its production line, significantly reducing waste and errors while increasing output. By utilizing rotary die cutting technology, they could produce high volumes of packaging materials without sacrificing quality or incurring additional costs.
Another example is a medical device manufacturer that applied precision die cutting to create custom gaskets and seals that met stringent regulatory standards. The result was not only a significant reduction in production times but also improved product reliability, leading to an increase in customer trust and market share.