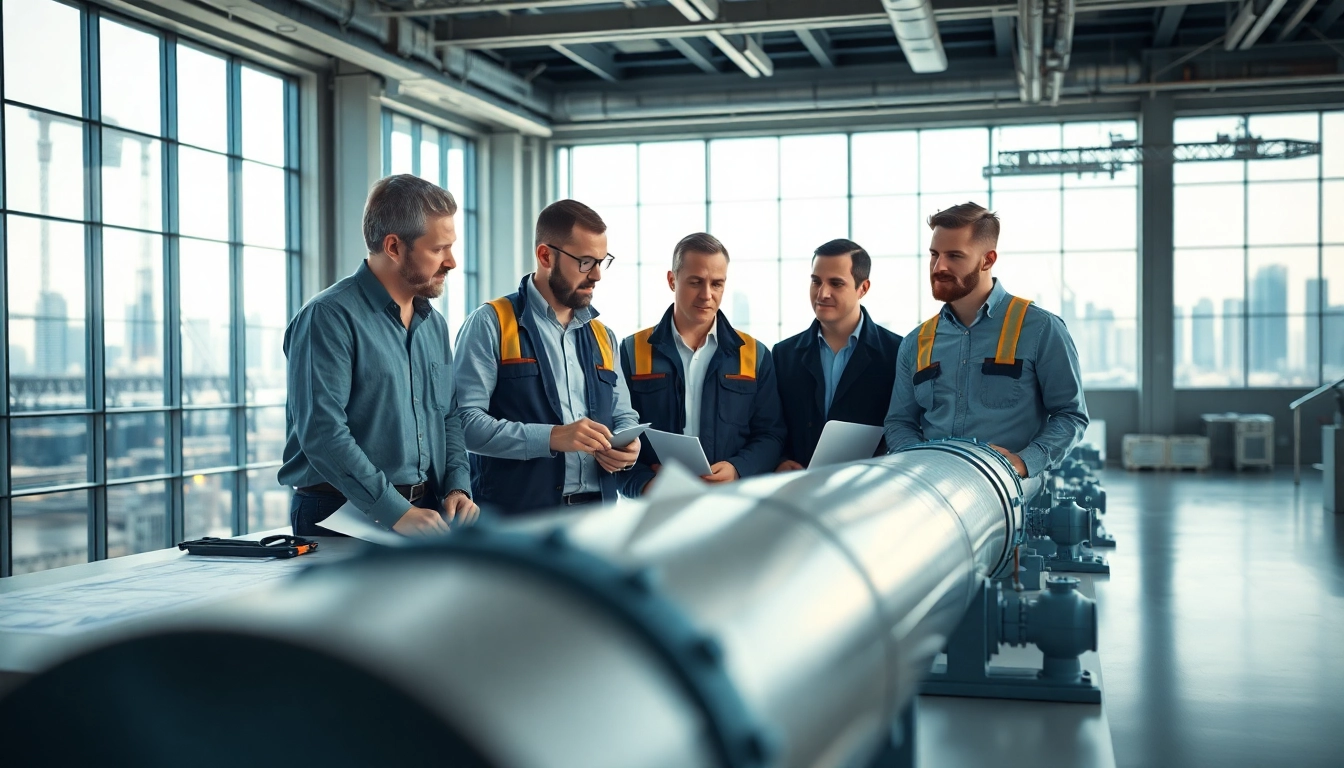
Understanding Pipe Stress and Its Importance
In engineering fields, the integrity of piping systems is critical, whether in oil and gas, pharmaceuticals, or food processing. Proper management of pipe stress is essential for ensuring the safety and longevity of these systems. A well-versed pipe stress company can provide invaluable support in this regard. Understanding pipe stress allows engineers to prevent failures that could lead to catastrophic accidents, costly repairs, and environmental issues. In this article, we’ll dive deep into the significance of pipe stress management, the challenges involved, best practices, real-world case studies, and future trends.
What is Pipe Stress?
Pipe stress refers to the strain experienced by piping systems due to various loading conditions and environmental factors. Mechanical forces, temperature variations, and gravity can all exert stress on pipes, leading to deformation and potential failure. Pipe stress analysis involves evaluating the response of piping systems to these loads and ensuring they remain within established safety limits. Effective analysis takes into account the pipe material, operating conditions, and the environment in which the system operates.
Key Factors Affecting Pipe Stress
Several crucial factors come into play in the determination of pipe stress:
- Temperature Variations: Changes in ambient temperature can cause pipes to expand or contract, leading to stress accumulation.
- Pressure Fluctuations: Variations in internal pressure can induce significant loads on the pipe walls, affecting structural integrity.
- Dead Loads and Live Loads: The weight of the piping itself (dead load) and dynamic forces from flowing fluids (live load) must be accurately calculated to assess stress.
- Support and Restraint Conditions: The way pipes are supported and restrained can greatly influence how stress impacts the system.
- External Factors: Environmental conditions, including seismic activity and ground movements, can add unexpected stress to piping systems.
The Role of a Pipe Stress Company in Engineering
A pipe stress company plays a pivotal role in ensuring the safety and reliability of piping systems. Their expertise encompasses analyzing the expected stresses and identifying locations that may require additional reinforcement or redesign. These companies employ sophisticated software packages and analytical methods to simulate various scenarios, ensuring that the pipeline will comply with industry standards and regulatory requirements. Moreover, their knowledge extends to choosing the right materials and designing operational practices that mitigate stress risks.
Common Challenges in Pipe Stress Analysis
Identifying Critical Stress Points
One of the most significant challenges in pipe stress analysis is identifying critical stress points. These points are locations where stress concentrations could lead to fractures or failures if not managed. Through finite element analysis (FEA) and other advanced techniques, engineers can pinpoint these areas, but it requires meticulous attention to detail, knowledge of material properties, and an understanding of fluid dynamics.
Impact of Temperature Changes
Temperature changes can dramatically affect pipe stress levels. Expansion and contraction cycles can induce fatigue in materials, leading to failures over time if the pipes are not designed to accommodate such changes. Engineers must factor in temperature fluctuations during all phases of design and construction, ensuring that suitable materials and fittings are used to minimize stress.
Material Limitations and Considerations
Choosing the right material for piping systems is crucial, not only for performance but also for managing stress effectively. Different materials exhibit unique stress-strain relationships and thermal expansions. Engineers must consider the limitations of these materials under expected load conditions, including yield strength and ductility, ensuring that the selected materials can withstand both static and dynamic loads without exceeding stress limits.
Best Practices for Effective Pipe Stress Management
Regular Monitoring and Maintenance Techniques
Implementing a regular monitoring and maintenance regime is essential for effective pipe stress management. Utilizing technology such as strain gauges and pressure sensors can provide real-time data on pipe performance, allowing engineers to identify potential stress issues before they escalate. Routine inspections should also be conducted to check for signs of wear, corrosion, or other factors that could compromise the structural integrity of the piping system.
Utilizing Advanced Software Tools
The advancement of software tools has revolutionized pipe stress analysis, allowing for more precise simulations of different load scenarios. Programs like CAESAR II, ANSYS, and AutoPIPE enable engineers to perform complex calculations and visualize stress distributions across the piping system. Utilizing these tools can lead to more informed decisions and proactive risk management strategies.
Collaboration with Qualified Pipe Stress Companies
Working alongside a qualified pipe stress company can lead to improved outcomes in stress analysis and management. These professionals bring a wealth of experience and knowledge, providing insights into best practices and innovative engineering solutions. Collaborating can also facilitate compliance with relevant regulatory standards, ensuring that piping systems are designed and maintained to meet safety criteria.
Case Studies: Successful Pipe Stress Management
Industry-Specific Applications
Many industries have successfully implemented comprehensive pipe stress management strategies, illustrating best practices and lessons learned. In the energy sector, for instance, companies have used advanced monitoring techniques that integrate real-time data analytics to minimize downtime caused by pipe failures.
Lessons Learned from Engineering Projects
Throughout various projects, teams have discovered critical lessons that enhance future pipe stress management. A notable example includes an oil refinery that experienced a major leak due to undersized piping. Post-incident analysis led to redesigned systems based on accurate thermal and pressure data, which improved efficiency and safety standards significantly.
Cost-Benefit Analysis of Professional Services
While engaging professional services from a pipe stress company may involve upfront costs, a thorough cost-benefit analysis often reveals significant long-term savings. Proper stress management reduces the risk of costly repairs, environmental damage, and lost operational time due to failure or leaks. In addition, the value of maintaining compliance with industry regulations cannot be overstated as penalties can be severe.
Future Trends in Pipe Stress Testing
Emerging Technologies in Analysis Methods
The future of pipe stress testing is likely to be shaped by advancements in emerging technologies such as machine learning and artificial intelligence. By leveraging these technologies, engineers can improve predictive analytics, allowing for more accurate forecasting of when and where pipe stress might lead to failure. This proactive approach can extend the life of piping systems and enhance operational safety.
Integrating IoT for Real-Time Monitoring
The Internet of Things (IoT) offers remarkable opportunities for real-time monitoring of pipe systems. Sensors connected through IoT can provide constant feedback on stress levels, temperature, and flow rates, ensuring that any deviations from normal operating conditions are addressed immediately. This real-time data stream can be integrated into a centralized platform for easy analysis and management, leading to timely interventions and optimized performance.
Adapting to New Regulatory Standards
As industries evolve, so do regulatory standards governing pipe stress management. Companies will need to stay abreast of changes in regulations and ensure their systems meet or exceed these requirements. Adapting to new standards may involve investment in new technologies and training for personnel, reinforcing the importance of collaboration with experienced pipe stress companies to navigate these challenges effectively.