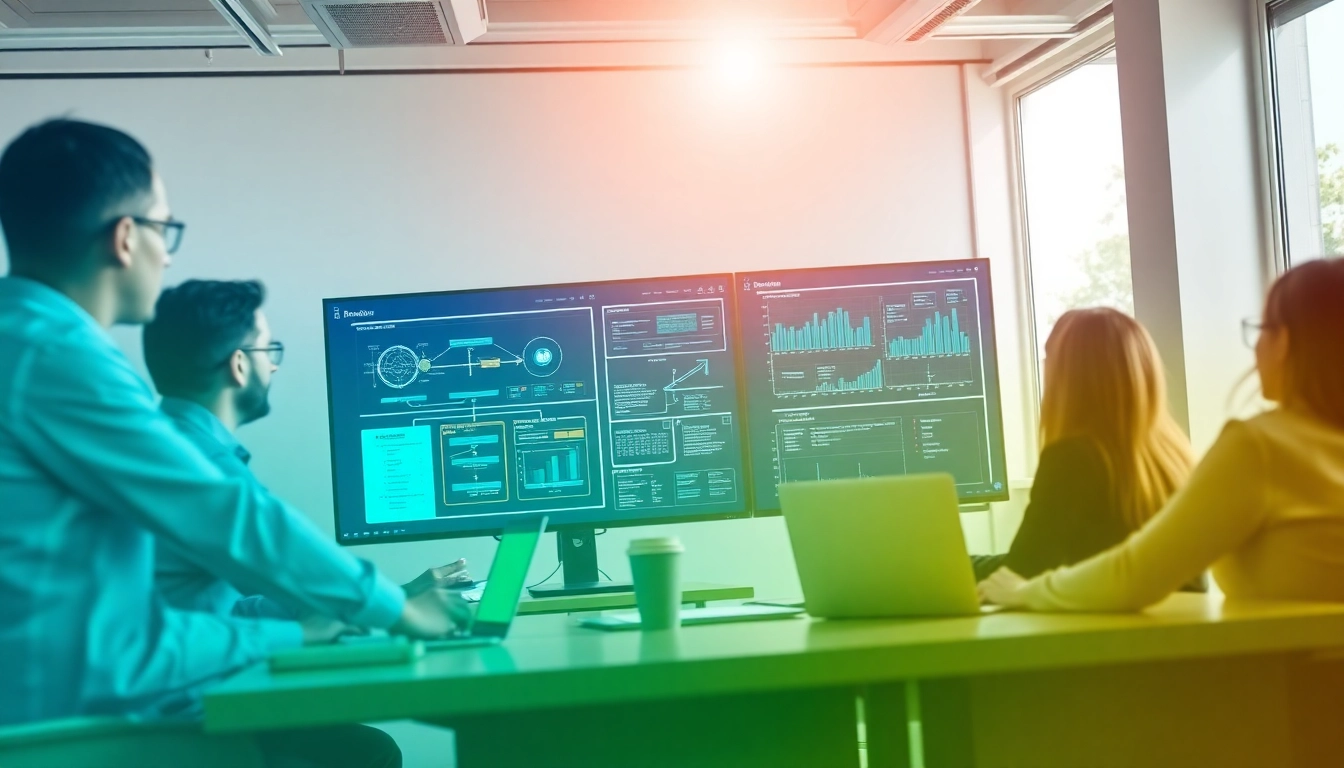
Understanding Process Optimization
Defining Process Optimization and Its Importance
Process optimization refers to the method of improving a process to make it more efficient and productive. In various sectors—from manufacturing to services—this approach minimizes waste, reduces operational costs, and enhances output. By refining the process, organizations can achieve higher quality results and maximize their resources effectively.
One of the pivotal reasons to engage in process optimization is the direct correlation between efficient processes and profitability. Organizations that focus on optimizing their processes adapt better to market demands, innovate faster, and ultimately gain a competitive edge.
Common Misconceptions About Process Optimization
There are several misconceptions surrounding process optimization. One prevalent myth is that it only applies to large organizations; however, even small enterprises can benefit significantly from process optimization by identifying inefficiencies unique to their operations. Another misconception is that process optimization merely equates to reducing costs. While cost reduction is crucial, optimization should also focus on enhancing quality and productivity.
Furthermore, many believe that process optimization is a one-time endeavor. In reality, it demands an ongoing commitment to continuous improvement and adaptation based on changing circumstances and new opportunities.
The Role of Data in Process Optimization
Data is a fundamental element in process optimization. Analytics derived from various processes can reveal insights about inefficiencies and bottlenecks, allowing organizations to make informed decisions on improvements. Techniques such as statistical analysis, process mapping, and performance metrics are essential in identifying areas needing attention.
The integration of big data into processes can enhance optimization efforts significantly. For example, real-time data can provide instantaneous feedback on operations, enabling businesses to adjust quickly. By fostering a culture that incorporates data-driven decision-making, organizations can achieve sustained improvements in their processes.
Key Principles of Process Optimization
Identifying Bottlenecks and Waste
Identifying bottlenecks is critical in the optimization journey. A bottleneck is a stage in a process that limits overall output; addressing it can lead to substantial efficiency gains. Tools such as value stream mapping help visualize the entire process, making it easier to locate these bottlenecks.
In addition, recognizing waste—be it in time, materials, or resources—is vital. A popular methodology for waste identification is the Lean approach, which categorizes waste into several types, including overproduction, waiting time, and excess motion. By systematically eliminating these inefficiencies, organizations can streamline their workflows significantly.
Streamlining Workflows for Improved Performance
Streamlining workflows is about creating a seamless process that maximizes efficiency. This typically involves standardizing procedures, reducing steps, and ensuring clarity in roles and responsibilities. Techniques such as process re-engineering often play a vital role in transforming existing workflows into more efficient frameworks.
For instance, implementing automation tools in repetitive tasks can dramatically speed up processes and minimize human error. The journey to a more streamlined workflow starts with careful analysis and adjustment of existing procedures, ultimately leading to enhanced performance and reduced operational costs.
Utilizing Technology to Facilitate Optimization
Emerging technologies play a crucial role in facilitating process optimization. Automation software, for example, can take over mundane tasks, allowing employees to focus on more strategic responsibilities. Process tracking tools provide instant feedback on performance and highlight areas for improvement.
Additionally, technologies such as artificial intelligence and machine learning present incredible potential for optimizing processes. These tools can analyze vast amounts of data to predict trends, optimize resource allocation, and enhance decision-making processes. Investing in technology is not just about adopting the latest trends; it’s about finding tools that specifically match your operational needs.
Implementing Process Optimization Strategies
Step-by-Step Guide to Analyzing Existing Processes
Analyzing existing processes is the first step toward effective optimization. Here’s a systematic approach:
- Define Objectives: Clearly specify what you hope to achieve through optimization—be it cost reduction, faster service delivery, or improved quality.
- Map Processes: Visualize current processes to understand the workflow, including roles and input/output.
- Collect Data: Gather quantitative and qualitative data related to performance metrics.
- Identify Areas for Improvement: Analyze the data for bottlenecks and inefficiencies.
- Develop and Implement Solutions: Formulate strategies based on your analysis, then implement them.
- Monitor and Adjust: Continuously track performance metrics regarding the new changes and make adjustments as necessary.
Engaging Team Members in the Optimization Effort
The success of any optimization effort heavily relies on the engagement of team members. Involving employees at every stage—from analysis to implementation—fosters a culture of continuous improvement and innovation. Conducting training sessions can equip them with the necessary skills for optimizing processes.
Creating a feedback loop is also crucial. Encourage team members to share their experiences and suggestions on the process improvements. This valuable input can lead to more effective and practical optimization strategies, as those who are directly involved know the nuances of the processes best.
Measuring Success Post-Implementation
Once process optimization strategies have been implemented, it is crucial to assess their effectiveness. This involves comparing pre- and post-implementation metrics. Key performance indicators (KPIs), such as cycle time, quality rates, and customer satisfaction scores, provide quantifiable data to evaluate success.
Regular review sessions should be established to discuss the performance data and overall efficiency. These sessions not only provide insights into what’s working but also encourage a culture of continuous improvement and adaptation to changing conditions.
Tools and Techniques for Effective Optimization
Overview of Popular Process Optimization Tools
Several tools can aid process optimization efforts. Here’s a brief overview of some effective tools:
- Value Stream Mapping: This tool visualizes workflows to identify waste and bottlenecks.
- Kaizen: A continuous improvement methodology focused on small, incremental changes.
- Business Process Model and Notation (BPMN): A graphical representation of business processes that provides clarity and standardization.
- Project Management Software (e.g., Trello, Asana): Helps organize tasks and monitor progress.
Lean vs. Six Sigma: Which Method Works Best?
Lean and Six Sigma are two prominent methodologies for process optimization. Lean focuses on reducing waste and improving workflow efficiency, while Six Sigma aims to reduce variability and improve process quality. Both methods offer valuable insights but can be most powerful when integrated into a comprehensive optimization strategy.
Organizations should assess their specific needs and challenges to determine which method suits them best. Factors such as company size, industry, and current challenges can influence this decision. Many companies effectively combine both approaches, utilizing Lean’s efficiency tactics alongside Six Sigma’s quality control measures.
Real-world Examples of Successful Process Optimization
Numerous companies have successfully implemented process optimization strategies. For example, Toyota’s production system emphasizes continuous improvement and efficiency, relying heavily on Lean principles. By minimizing waste and focusing on quality, Toyota has consistently elevated its market position.
Similarly, General Electric (GE) adopted Six Sigma in the late 1990s, leading to significant reductions in defects, operational costs, and project cycles. These examples showcase how tailored optimization methods can lead to substantial organizational benefits, setting benchmarks within the industry.
Future Trends in Process Optimization
The Growing Importance of AI and Automation
As technology evolves, the role of artificial intelligence in process optimization grows increasingly significant. With AI, businesses can analyze data more efficiently, predict issues before they arise, and automate repetitive tasks to free up resources for higher-value work. This trend toward smart automation will reshape how businesses approach optimization strategies.
Moreover, machine learning algorithms can learn from each interaction, continuously enhancing their ability to optimize processes over time without requiring extensive human intervention.
Emphasizing Sustainability in Process Optimization
In light of growing environmental concerns, integrating sustainability into process optimization is becoming necessary. Companies that consider their ecological footprint while optimizing processes can gain a competitive edge. Sustainable practices, such as reducing energy consumption and optimizing supply chain logistics, are now a focal area for modern businesses.
Emphasizing sustainability not only addresses regulatory pressures but also appeals to increasingly eco-conscious consumers, creating a win-win scenario for both businesses and the planet.
Preparing Your Organization for Future Challenges
Organizations should cultivate a mindset of adaptability and resilience to tackle future challenges that may arise in process optimization. This involves embracing change and investing in employee training, skills development, and technological advancements.
Building a culture that values innovation and flexibility will allow businesses to respond swiftly to new challenges and leverage opportunities as they arise. As the landscape of industries continues to evolve, ongoing evaluation and proactive adjustments in process optimization will ensure long-term success.