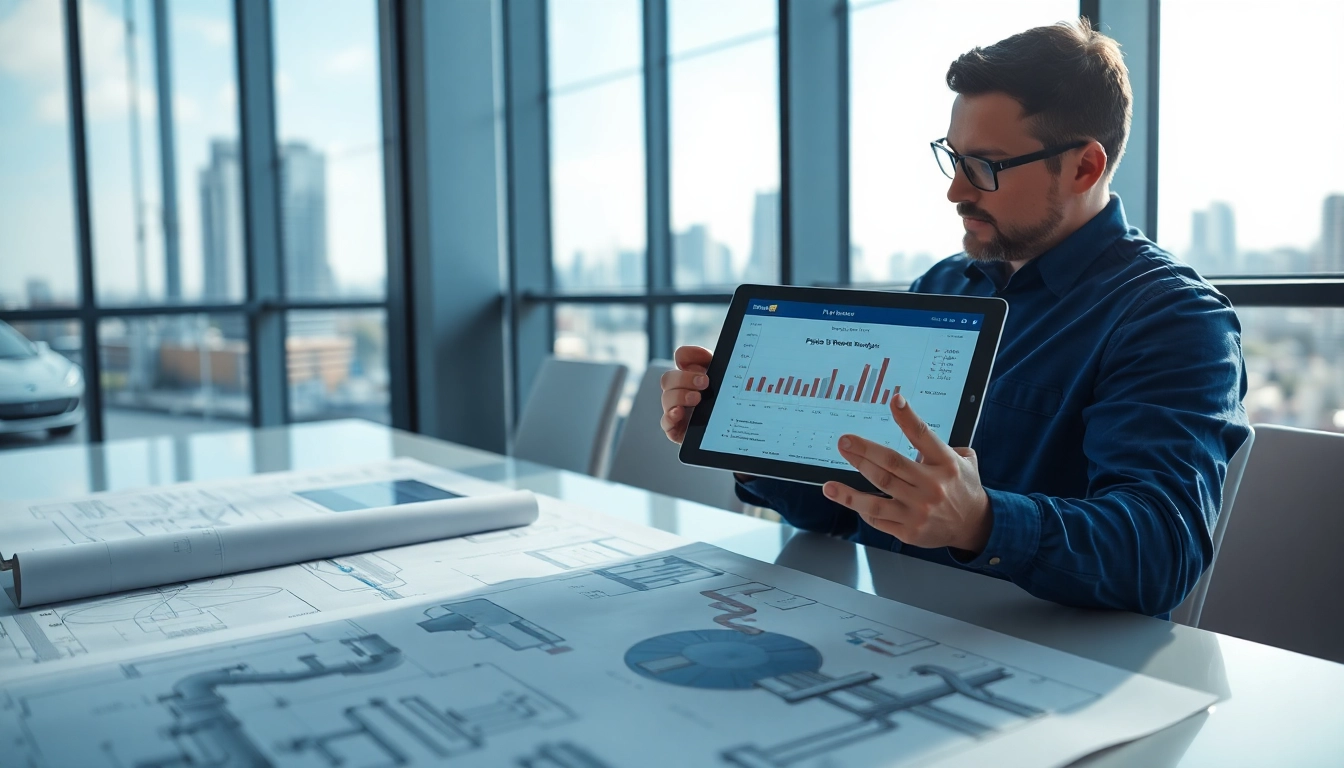
Understanding Pipe Stress Analysis
What is Pipe Stress Analysis?
Pipe stress analysis is a crucial engineering discipline focused on assessing the mechanical behavior of piping systems under various operational conditions. The analysis involves evaluating the stresses and deformations that occur as a result of thermal expansion, pressure variations, vibration, and external loads. By understanding these factors, engineers can ensure that piping systems can withstand the pressures and stresses exerted on them over time without failure.
This analysis is typically conducted using sophisticated software that simulates the physical properties and operational conditions of pipeline installations. The objective is to ensure the integrity and safety of the piping system throughout its operational life while adhering to codes and standards. The complexity of pipe stress analysis requires collaboration between various engineering disciplines, making it essential for industries reliant on robust piping systems.
Importance of Pipe Stress Companies
Pipe stress companies play a pivotal role in the design, implementation, and maintenance of piping systems across numerous sectors. They specialize in the rigorous analysis required to prevent catastrophic failures, ensuring not only the safety of personnel but also the preservation of equipment and the environment. Their expertise is crucial for managing potential issues that can arise from pipe stress, including bends, thermal expansion, and vibration.
A reliable pipe stress Company will evaluate both static and dynamic loads on piping systems, assisting industries such as oil and gas, power generation, chemical processing, and water treatment. By ensuring the structural integrity of piping systems, these companies help mitigate risks associated with leaks, ruptures, and maintenance costs, thereby enhancing overall operational efficiency.
Common Applications in Industries
The applications of pipe stress analysis span various industries, each with distinctive requirements and challenges. In the oil and gas sector, for example, the extraction and transportation of hydrocarbons through extensive piping networks demand meticulous stress evaluation to prevent leaks and ensure safe operations. Similarly, in the power generation industry, high-pressure steam pipelines need to be analyzed to withstand thermal expansion and contraction during operation.
In the chemical processing industry, where aggressive substances may be transported through pipelines, stress analysis is critical to prevent material degradation and ensure safety protocols are followed. Water treatment facilities also prioritize pipe stress analysis to handle varying flow rates and pressures, safeguarding infrastructure and supporting compliant operations. Each of these sectors benefits from tailored stress analysis strategies to optimize asset management and reduce operational risks.
Key Factors Affecting Pipe Stress
Material Properties and Their Impact
The material selection for piping systems is fundamental to successful pipe stress management. Different materials exhibit varying physical properties, such as tensile strength, yield strength, and ductility, all of which impact how the pipe behaves under stress. For instance, steel has a high tensile strength but may become brittle under certain temperature conditions, while plastic pipes are more flexible but may have lower pressure ratings.
When analyzing pipe stress, engineers must consider the material’s modulus of elasticity and thermal expansion coefficient, which dictate how the material reacts to temperature changes. These properties not only influence the design of pipeline systems but also affect maintenance schedules and operational strategies. It’s essential for engineering teams to employ materials that align with the specific operational conditions expected throughout the lifespan of the piping system.
Temperature Effects on Pipeline Systems
Temperature fluctuations can significantly impact pipeline systems, causing thermal expansion or contraction, which leads to changes in stress levels within the pipes. For instance, in environments where temperatures vary widely, the differential expansion of materials may cause excessive stress at joints, leading to cracks or leaks.
Engineers must consider the operating temperature range while performing pipe stress analysis. This includes understanding the thermal profile of the pipeline—how it expands when heated and contracts as it cools—which is critical for designing supports, anchors, and expansion joints. Anticipating these temperature-related stressors enables companies to proactively address potential issues and maintain the integrity of their piping systems.
Load Assessments for Safety
Load assessments are integral to identifying the forces acting on a pipeline, which include dead loads (the weight of the pipe and its contents), live loads (dynamic forces, such as wind or seismic activity), and occasional loads (such as maintenance activities). Each of these loads contributes to the overall stress that the pipe must endure.
By accurately assessing these loads during the stress analysis process, engineers can implement the necessary design modifications to withstand these conditions. This can involve the incorporation of clamps, braces, or other supports that help distribute loads evenly and minimize excessive stress. The goal is to maintain safety and compliance with industry standards, ultimately protecting both personnel and physical assets.
Best Practices for Effective Pipe Stress Management
Choosing the Right Pipe Stress Company
Selecting a capable pipe stress company is imperative for achieving effective stress analysis and management. Companies should evaluate potential partners based on their experience, technical expertise, and previous project outcomes. Recommended practices include asking for case studies or references that demonstrate the company’s proficiency in relevant industries.
Moreover, reviewing the technologies and software used by the pipe stress company can offer insights into their analytical capabilities. Advanced tools can generate more accurate simulations, helping to identify potential stress points before they become critical issues. Ultimately, a well-chosen partner can make a significant difference in ensuring the safety and reliability of piping operations.
Implementing Regular Stress Testing
Regular stress testing is essential for maintaining the integrity of piping systems, especially in industries where operational conditions change frequently. By conducting periodic evaluations, companies can identify wear and tear or unforeseen stress factors early. This proactive approach allows for timely interventions that can prevent costly repairs and operational downtimes.
Moreover, integrating stress testing into the maintenance schedule encourages adherence to safety protocols and builds a culture of responsibility within an organization. Documenting test results also provides valuable data for future projects and helps establish a knowledge base for best practices in pipe stress management.
Adopting Advanced Simulation Technologies
Advanced simulation technologies have revolutionized the field of pipe stress analysis. Software tools can now create detailed models of pipe systems, allowing for comprehensive simulations under various operational scenarios. These technologies enable engineers to visualize stress distributions and predict fail points with greater accuracy than traditional methods.
Moreover, adopting such technologies can facilitate collaboration among engineering teams, ensuring that all stakeholders are informed and involved in the decision-making process. Investing in training for these technologies can also lead to more efficient workflows and improved outcomes for piping projects. As the industry evolves, staying abreast of technological advancements is vital for maintaining a competitive edge in pipe stress management.
Case Studies: Successful Pipe Stress Management
Industry-Specific Challenges and Solutions
Across various industries, unique challenges arise that require tailored solutions for effective pipe stress management. For instance, in the oil and gas sector, complex offshore installations face severe environmental loads, necessitating robust stress analysis to guard against extreme weather conditions and equipment fatigue. In one case, a leading oil company partnered with a pipe stress company to redesign pipeline supports, integrating dynamic analysis to account for wave and wind loads.
This approach yielded notable success, enhancing system stability and reducing maintenance costs over time. Such case studies highlight how industry-specific challenges can be effectively managed through specialized strategies rooted in comprehensive analysis and innovative solutions.
Long-term Benefits for Companies
Implementing steady pipe stress management practices offers significant long-term benefits for companies. Thoughtful stress analysis leads to a decrease in pipeline failures, ensuring operational continuity and heightened safety. Over time, companies that prioritize stress management enjoy reduced repair costs and longer asset lifespans.
Furthermore, a strong reputation for safety can open new market opportunities, attracting clients who prioritize compliance with safety and regulatory standards. Long-term investments in pipe stress analysis, therefore, not only protect existing assets but also foster business growth and resilience.
Lessons Learned from Major Projects
Lessons learned from major pipeline projects often emphasize the importance of thorough pre-construction pipe stress analysis. One significant lesson from a large-scale chemical plant construction highlighted the repercussions of inadequate stress evaluation, which resulted in unplanned maintenance and downtime. By analyzing failure points after completion, the project team was able to refine their stress analysis methodologies for future installations.
This iterative approach to learning ensures that advancements in technology and practices are incorporated, optimizing the effectiveness of stress management techniques as the industry continues to evolve. Documenting challenges and successes serves as an invaluable resource for future projects, enhancing collective knowledge and influencing industry standards.
The Future of Pipe Stress Analysis
Emerging Technologies in Pipe Stress Management
The future of pipe stress analysis is promising, with numerous emerging technologies poised to enhance the field. Predictive analytics powered by machine learning can analyze vast datasets, enabling companies to forecast potential failures before they occur. Additionally, 3D modeling and augmented reality tools facilitate immersive simulations, allowing engineers to visualize and assess stress factors in real time.
The integration of Internet of Things (IoT) sensors into piping systems is also reshaping how stress analysis is conducted. These sensors can provide continuous monitoring, delivering real-time data on temperature fluctuations and load changes, which can give new insights into stress behavior over time. Such innovations highlight the shift toward proactive management of piping systems, reducing reliance on reactive maintenance efforts.
Regulatory Changes and Industry Standards
The regulatory landscape surrounding pipe stress analysis is constantly evolving, with new standards and codes emerging to address the complexities of modern industrial needs. Companies must stay updated on these changes to maintain compliance and ensure that their practices align with industry best practices.
Regulations often dictate specific methodologies for stress analysis, prompting companies to adapt their approaches to meet compliance requirements. Proactive engagement in industry forums and collaborations can equip companies with the knowledge needed to navigate these changes effectively, ensuring that their stress management practices remain current and effective.
Collaboration between Engineers and Pipe Stress Companies
The future of effective pipe stress management relies heavily on strong collaboration between engineers and pipe stress companies. By fostering open communication and sharing insights early in project planning, all stakeholders can align on objectives and methodologies. This collaborative approach leads to more effective stress analysis and better project outcomes.
Joint workshops and training sessions can facilitate knowledge sharing, allowing engineers and specialists to learn from one another. As the industry becomes increasingly reliant on technological innovations, such partnerships will be key in maximizing the benefits of both human expertise and advanced analytical tools in managing pipe stress effectively.