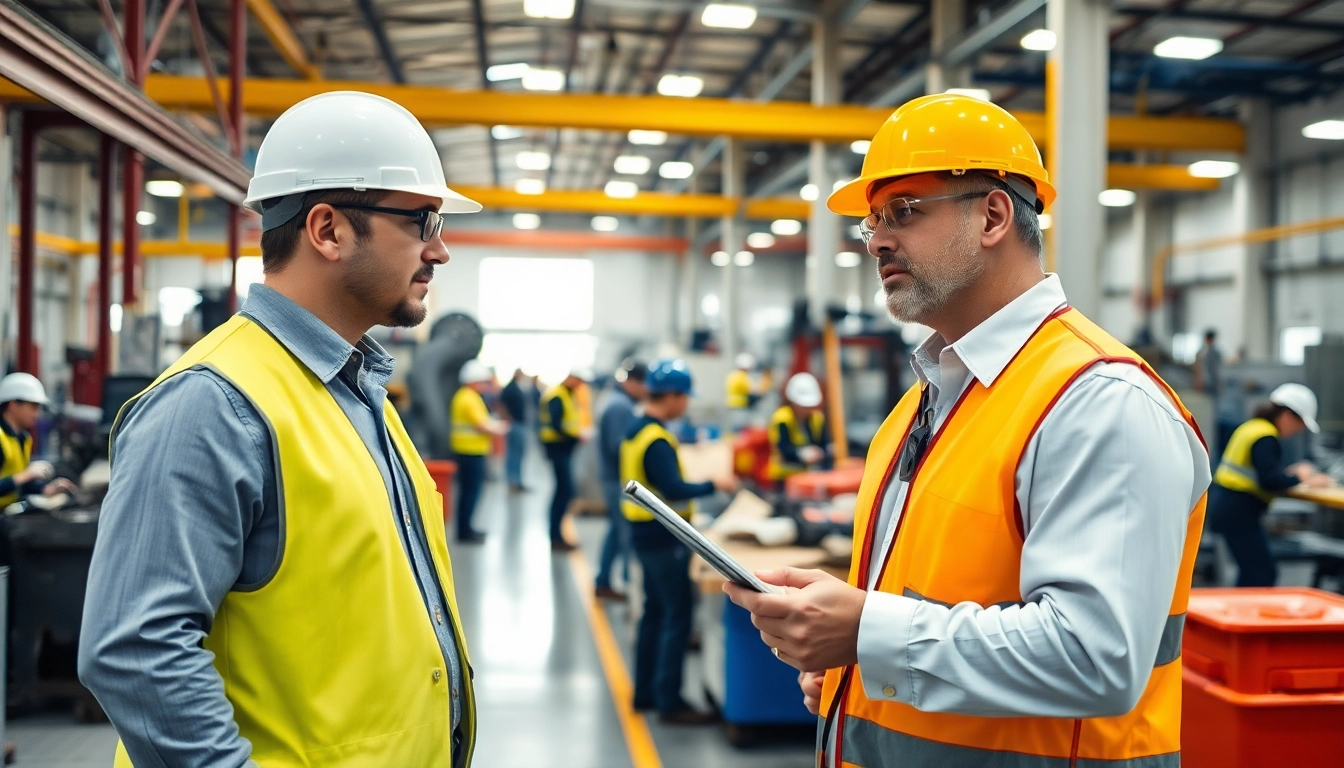
Understanding Workplace Safety Audits
What is a Workplace Safety Audit?
A workplace safety audit is a systematic assessment that aims to identify hazards and risks within a work environment. This process also evaluates whether existing safety measures align with industry standards and regulatory requirements. Safety audits are crucial in promoting a reliable, efficient, and effective safety culture, and they gather valuable information regarding an organization’s overall safety performance.
Conducting a thorough Workplace Safety Audit not only ensures compliance but also enhances employee morale, reduces incident rates, and protects the organization from potential liability claims. In essence, safety audits are not merely a regulatory procedure but serve as an essential strategic tool for maintaining a safe workplace.
Importance of Conducting Safety Audits
The significance of safety audits cannot be overstated. They provide a detailed insight into various workplace conditions and practices, enabling organizations to:
- Detect Hazards: Safety audits help in early identification of workplace hazards, reducing the chance of accidents and incidents.
- Improve Compliance: Regular audits ensure adherence to legal requirements and safety regulations, minimizing regulatory risks.
- Enhance Safety Culture: By actively engaging employees in safety discussions, organizations propagate a culture of safety awareness.
- Optimize Resources: Audit findings can guide efficient resource allocation, ensuring that safety measures effectively target the most critical risks.
Common Misconceptions about Safety Audits
Despite the clear benefits of safety audits, several myths persist that hinder their effective implementation:
- Only for Large Organizations: Many small and medium-sized enterprises (SMEs) often believe safety audits are only necessary for large corporations. In reality, all businesses, regardless of size, must prioritize safety.
- One-time Event: Some companies approach audits as a one-off activity rather than integrating them into their regular safety protocols. Safety audits should be routine to enhance ongoing safety performance.
- Too Costly: Companies often view audits as an expense rather than an investment. The cost of accidents far exceeds the costs incurred during audits, making them financially prudent.
Preparing for a Workplace Safety Audit
Key Steps to Prepare
Preparing for a workplace safety audit requires an organized approach:
- Inform Stakeholders: Notify relevant personnel, including safety teams, supervisors, and managers, about the impending audit. Clear communication is crucial for effective preparation.
- Review Past Audits: Examine previous audit results and ensure recommended actions were implemented. This provides a baseline and ensures continual improvement.
- Determine the Audit Scope: Establish the parameters and focus areas for the audit, considering higher-risk projects or areas that have reported incidents.
Assigning Responsibilities and Roles
Effective audits depend on clear allocation of responsibilities. The following roles should be defined:
- Lead Auditor: This individual oversees the audit process, coordinates tasks, and ensures timely completion.
- Team Members: Select team members with diverse expertise to bring various perspectives during the audit.
- Stakeholder Involvement: Involve employees at all levels to gain insights from their daily experiences and observations.
Gathering Necessary Documentation
Document collection is a vital preparation step. Key documents may include:
- Previous safety audit findings and corrective action reports.
- Incident and accident reports.
- Safety policies and procedures.
- Training records and compliance certificates.
This documentation lays the groundwork for a thorough and informed audit process.
Conducting the Workplace Safety Audit
Types of Safety Audits Explained
Understanding the different types of safety audits can help in selecting the most effective approach for a workplace:
- Compliance Audits: Focus primarily on adherence to legal and regulatory standards.
- Program Audits: Review the effectiveness of safety programs and initiatives within the organization.
- Management System Audits: Assess the overarching safety management framework, including policies, procedures, and leadership engagement.
Step-by-Step Audit Process
The audit process can be broken down into several key steps:
- Preparation: As previously outlined, proper preparation is critical.
- On-Site Inspection: Conduct thorough inspections of workplaces, evaluating equipment, processes, and employee practices.
- Employee Interviews: Engage with employees to understand their perspective on safety practices and potential hazards.
- Document Findings: Systematically record observations and notable incidents during the audit.
- Reporting: Compile the audit results in a clear format that outlines findings, conclusions, and recommendations.
Tools and Resources for Effective Audits
Leveraging the right tools enables a more efficient audit process. Consider utilizing:
- Safety Audit Checklists: These checklists provide a structured framework to ensure no critical area is overlooked.
- Software Solutions: Digital tools can streamline data collection and reporting processes.
- OSHA Guidelines: Familiarize yourself with Occupational Safety and Health Administration (OSHA) requirements to ensure compliance.
Analyzing Audit Findings
Documenting Results and Observations
After the audit is conducted, the next critical step is to collate and document findings. This should include:
- Observations regarding compliance and non-compliance.
- Identified hazards and risks associated with workplace activities.
- Employee insights and suggestions from interviews conducted during the audit.
Identifying Actionable Insights
From the documented findings, it’s crucial to derive actionable insights. This involves analyzing data to:
- Prioritize hazards based on risk level.
- Identify trends in incidents or near-misses that point to systemic issues.
- Evaluate the efficacy of existing safety measures.
Addressing Compliance Issues
When compliance issues are identified, they must be addressed through corrective action plans. This includes:
- Developing specific actions to rectify identified non-compliance issues.
- Setting deadlines and responsible parties for each corrective action.
- Establishing metrics to evaluate the effectiveness of corrective measures post-implementation.
Implementing Recommendations and Follow-up
Creating an Action Plan
An action plan is essential for translating audit findings into tangible improvements. Key elements to include are:
- Clear timelines for each action.
- Responsible individuals for tracking and facilitating actions.
- Checklist of necessary resources for implementing changes.
Engaging Employees in Safety Practices
Employee involvement is pivotal in fostering a culture of safety. Consider implementing:
- Training Programs: Offer regular training to keep safety practices fresh in employees’ minds.
- Feedback Mechanisms: Establish channels for employees to give feedback on safety practices and procedures.
- Incentives: Recognize and reward safe practices to motivate all employees to prioritize safety.
Scheduled Follow-ups for Continuous Improvement
Finally, conducting follow-ups ensures that safety practices continue to evolve. Key strategies include:
- Setting a regular schedule for future audits.
- Reviewing the effectiveness of corrective actions implemented.
- Encouraging ongoing communication about safety among staff.
In conclusion, a comprehensive workplace safety audit is essential for promoting a safe and compliant work environment. By understanding the audit process, preparing effectively, and following through with actionable recommendations, organizations can not only comply with regulations but also create a culture of safety that benefits everyone involved.