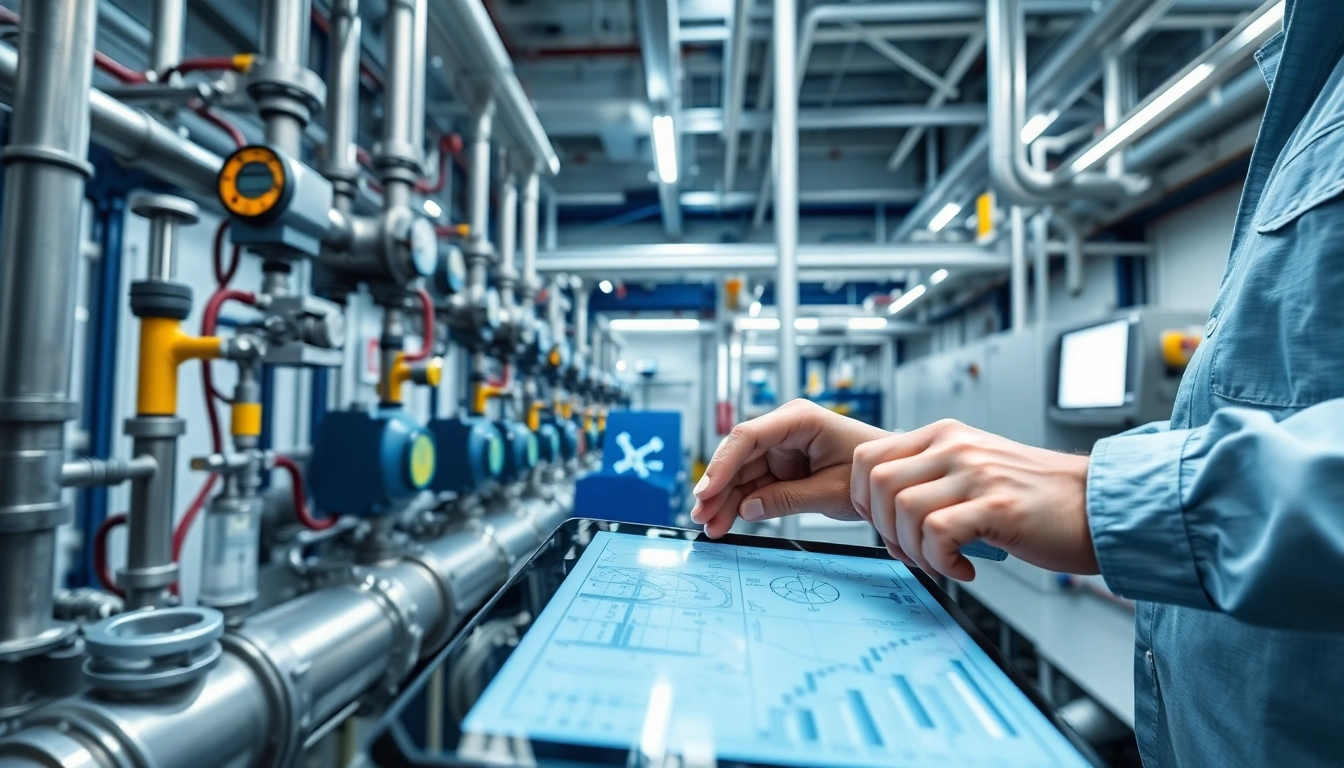
Understanding Pipe Stress Analysis
Pipe stress analysis is a crucial process in engineering that evaluates the stresses and deflections that occur in piping systems due to various external and internal loads. The fundamental objective of this analysis is to ensure that the mechanical integrity of pipes is maintained throughout the lifecycle of a project. Proper implementation of pipe stress analysis contributes significantly not only to the safety and reliability of the system but also to its overall efficiency. Those involved in projects ranging from industrial facilities to commercial infrastructure often need to engage with pipe stress analysis to mitigate potential failures and enhance the design process.
What is Pipe Stress Analysis?
Pipe stress analysis refers to the mathematical and computational examination of piping systems to determine how they respond to internal and external forces, temperature changes, and other operational conditions. It involves the use of various engineering principles, including the materials’ mechanical properties, the physical design of the piping, joint configurations, and support systems. The analysis generally takes into account several types of forces:
- Internal pressure: The pressure exerted by fluids within the pipe.
- Thermal expansion: Changes in pipe dimensions due to temperature variations.
- Weight of the pipe: The gravitational force acting on the piping including the effects of the contents.
- Inertia forces: Forces caused by changes in directional flow or motion.
By simulating these conditions, engineers can predict the behavior of the piping and identify any potential issues before they escalate into costly or dangerous failures.
The Importance of Pipe Stress Analysis in Engineering
The importance of pipe stress analysis cannot be overstated, particularly in industries such as oil and gas, chemical processing, and construction. Here are several reasons why pipe stress analysis is essential:
- Safety: Ensuring that pipes can withstand extreme conditions is paramount to prevent leaks or ruptures that can lead to hazardous incidents.
- Cost Efficiency: By identifying potential issues early in the design process, costly redesigns or late-stage modifications can often be avoided.
- Compliance: Many engineering standards and regulations mandate specific stress analysis procedures to ensure that the piping systems are resistant to failure.
- Performance Optimization: A well-analyzed piping system can operate more efficiently and with less maintenance, reducing overall lifecycle costs.
Main Techniques Used in Pipe Stress Analysis
Several techniques exist for conducting pipe stress analysis, which can vary depending on the complexity of the system being examined. These include:
- Hand Calculations: These involve simplified methods and formulas commonly used for smaller, straightforward systems. While quicker, they may overlook localized effects.
- Finite Element Analysis (FEA): A sophisticated computational method that uses numerical techniques to predict how a system responds to external forces. FEA is particularly beneficial for analyzing complex geometry.
- Computer Aided Design (CAD): Software tools that facilitate the modeling of piping systems, allowing for detailed visualization alongside stress analysis features.
By employing the right technique, engineers can achieve precise and reliable results that inform the further development of their piping designs.
Key Factors Influencing Pipe Stress
Various factors can greatly influence pipe stress, dictating how practitioners approach analysis and design. Understanding these factors is essential for implementing accurate and effective pipe stress analysis.
Material Selection and Properties
The selection of materials for pipes is foundational to managing stress effectively. Different materials respond uniquely to stress factors such as temperature changes, corrosion, and loads. Key properties of materials include:
- Yield Strength: This determines the point at which a material will deform plastically.
- Tensile Strength: This reflects the resistance of a material to breaking under tension.
- Thermal Conductivity: This influences how heat affects the materials’ dimensional stability and overall behavior under temperature fluctuations.
Choosing materials with suitable properties tailored to the specific environment and operational parameters is vital for long-term performance.
Temperature and Pressure Considerations
Temperature and pressure are two of the most significant contributors to pipe stress. Higher temperatures can lead to thermal expansion, while increased pressure may enhance the internal forces acting on the pipe walls. Engineers must consider:
- Operating Temperature Range: Understanding how materials react at different temperatures is vital for designing a safe system.
- Pressure Ratings: Each piping material has specific pressure limits that must be adhered to during operation.
When analyzing pipe systems, temperature and pressure factors must be included in calculations and simulations to avoid miscalculations leading to system failures.
Environmental Effects on Pipe Stress
Environmental conditions play a crucial role in the behavior of piping systems. Factors to consider include:
- Corrosion: Exposure to chemical or environmental conditions can lead to material degradation over time.
- Dynamic Loads: Effects from winds, seismic activity, or ground settling can introduce unexpected stresses.
- Moisture and Temperature Variations: Varying climate conditions can impose additional long-term stress on the piping system.
Understanding these environmental impacts allows engineers to incorporate adequate protective measures that ensure ongoing system integrity.
Challenges in Pipe Stress Analysis
Despite its importance, pipe stress analysis is rife with challenges that professionals must navigate carefully. Recognizing these challenges allows engineers to employ strategic solutions to ensure effective outcomes.
Common Issues Faced During Analysis
Some prevalent issues that can arise during pipe stress analysis include:
- Inaccurate Models: Early stages of modeling can lead to errors that manifest as unforeseen stress concentrations.
- Complex Interactions: Interactions between different sections, such as bends, valves, and fittings can create complexities that are hard to predict.
- Data Limitations: Insufficient or inaccurate data regarding materials and loads can result in poor analysis outcomes.
Addressing these challenges early through thorough checks and validations can significantly improve the reliability of the analysis.
Overcoming Design Constraints
Engineers often face various design constraints, including space limitations and existing infrastructures. Strategies to overcome these constraints include:
- Flexible Design Practices: Utilizing expansion joints and supports can mitigate thermal movement without compromising overall design integrity.
- Innovative Routing Solutions: Opting for horizontal versus vertical runs when advantageous can often help navigate space restrictions appropriately.
- Consulting with Stakeholders: Early engagement with all project stakeholders can unveil concerns that can be addressed in the design phase.
By adopting flexible strategies, engineers can better adapt their designs to existing constraints while maintaining safety and efficiency.
Accuracy vs. Complexity Trade-offs
A balance must often be struck between the complexity of models and the accuracy of results. Highly detailed analyses can provide incredibly precise information, but this often requires extensive computational resources and time while simplifying assumptions may reduce accuracy. Effective approaches may include:
- Sub-modeling Techniques: Breaking down complex sections into simpler models for focused analysis without overcomplicating the overall system.
- Adaptive Simulations: Utilizing dynamic simulations that adjust based on varying conditions can help manage trade-offs effectively.
Ultimately, it’s essential to find the right level of complexity that allows for meaningful results without overwhelming the analysis process.
Best Practices for Effective Pipe Stress Analysis
To achieve optimal results in pipe stress analysis, engineers should adhere to best practices that enhance precision and reliability. Implementing these practices can significantly aid in producing comprehensive analyses.
Utilizing Advanced Software Tools
Modern software tools enable engineers to conduct sophisticated analyses with ease. Tools such as Caepipe, AutoPIPE, and ANSYS provide advanced functionalities that allow for detailed modeling, simulation, and reporting. Engineers should:
- Stay Updated: Keeping abreast of software advancements can provide new functionalities that enhance analysis workflows.
- Training and Certification: Investing in proper training ensures that staff can effectively utilize tools to carry out complex analyses.
Leveraging advanced software helps in producing accurate predictions while also improving the efficiency of the workflow.
Conducting Thorough Risk Assessments
Risk assessments are critical in recognizing potential failures before they occur. Best practices for risk assessments include:
- Scenario Analysis: Running simulations for various failure conditions can help teams understand potential risks and devise mitigation strategies.
- Regular Maintenance Checks: Implementing ongoing evaluation processes of existing systems ensures that any issues are caught early, preventing catastrophic failures.
Thorough assessments fortify the integrity of the piping systems and the overall project safety.
Iterative Design Approach and Validation
Adopting an iterative design process allows for improved accuracy and learning from continuous feedback. This practice includes:
- Feedback Loops: Regular reviews and updates on system designs help assimilate lessons learned and improve subsequent iterations.
- Validation Testing: Conducting physical tests on prototypes can provide real-world data that enhances model accuracy.
Implementing an iterative approach helps ensure that design processes remain adaptable and improvements are consistently identified and integrated.
Case Studies and Real-World Applications
Understanding pipe stress analysis through real-world applications can provide invaluable insights into its practical relevance and implementation strategies. Case studies from various industries can illustrate typical challenges and solutions faced in pipe stress analysis.
Case Study: Oil and Gas Pipelines
In oil and gas industries, pipelines experience extreme conditions, including high pressures and temperatures, making pipe stress analysis vital. A major oil company undertook a comprehensive analysis when designing a large pipeline to transport crude oil over varying terrains.
- Challenge: The terrain included mountainous areas subject to seismic activities, placing additional stress on the pipelines.
- Solution: Enhanced FEA techniques were implemented to integrate seismic data into the stress analysis, leading to better support design and material selection.
- Result: The thorough analysis resulted in a resilient pipeline design that absorbed shocks from seismic events without resulting in failures.
Case Study: Chemical Processing Plants
A leading chemical manufacturer faced challenges in their plant due to severe chemical corrosion in their piping systems. Effective stress analysis was necessary to redesign existing pipelines to enhance longevity and reliability.
- Challenge: High corrosive environments which led to unforeseen crack formations in existing pipes.
- Solution: By applying an iterative design process, the company developed new pipe systems with corrosion-resistant materials while also automating the monitoring of stress points.
- Result: The new piping systems not only reduced the need for maintenance but also improved overall plant safety and operational efficiency.
Case Study: Infrastructure Projects
In a recent municipal infrastructure project involving water supply systems, traditional piping stress calculations underestimated the stresses due to unexpected load combinations.
- Challenge: Initial designs failed to consider winter freezing conditions which introduced additional pressures and expansion forces.
- Solution: The design team re-evaluated the entire system under critical winter conditions, employing detailed modeling and risk assessment to redesign sections of the pipeline.
- Result: The redesigned system successfully managed anticipated stresses, preventing costly failures and ensuring reliable water supply throughout the year.