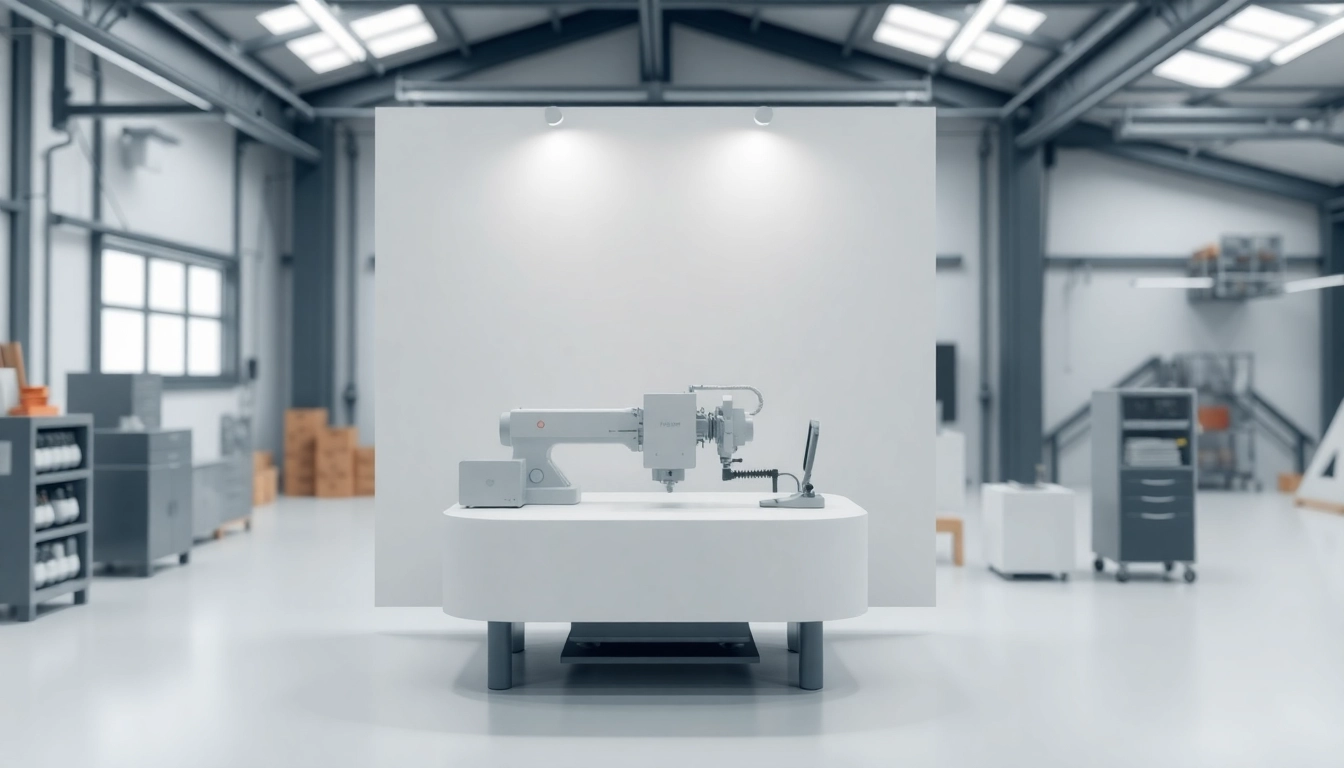
Understanding Liquid Packaging Technology
The landscape of manufacturing has evolved dramatically over the years, and one of the critical components of this evolution is liquid packaging technology. As industries expand and the demand for efficient packaging solutions increases, the role of a Liquid Packaging Machine Supplier becomes pivotal. Understanding how liquid packaging works and the factors influencing its technology can make a significant difference in your business operations.
What is Liquid Packaging?
Liquid packaging refers to the method of enclosing liquid products in containers for storage, transportation, and sale. This process involves using technology and machinery designed to handle various types of liquids, including water, beverages, chemicals, and pharmaceuticals. The objective is to protect the product from contamination, preserve its quality, and ensure it is convenient for consumers. Liquid packaging not only maintains the product’s integrity but also enhances marketing by allowing for brand-specific designs and information to be displayed on the packaging.
Types of Liquid Packaging Machines
Liquid packaging machines can be categorized based on their functionality and application. Here are some common types:
- Filling Machines: These are designed to accurately fill containers, such as bottles or pouches, with liquid products. They can operate manually or automatically, depending on the volume of production.
- Capping Machines: These machines apply caps to filled bottles or containers. They work in conjunction with filling machines to ensure that products are sealed securely.
- Labeling Machines: After filling and capping, labeling machines add product labels to containers, ensuring compliance with packaging regulations and enhancing brand visibility.
- Pouch Packing Machines: These are specialized machines for filling and sealing pouches. They are ideal for liquids that require reduced exposure to air.
- Blending Machines: These machines mix various liquids to produce a homogeneous product before packaging.
Industries Benefiting from Liquid Packaging
Numerous industries leverage liquid packaging, each demanding specific technologies suited to their products. Here are a few key sectors:
- Food and Beverage: This industry uses liquid packaging for sauces, juices, and dairy products. The packaging needs to maintain freshness and prevent spoilage.
- Pharmaceuticals: Liquid medications are packaged to ensure they remain sterile and effective. This industry demands high standards of accuracy and safety.
- Cosmetics: Liquids such as lotions and perfumes are systemically packaged to enhance user experience and safety.
- Chemicals: Packaging for industrial chemicals requires robust materials and designs to contain hazardous liquids safely.
Choosing the Right Liquid Packaging Machine Supplier
Finding a reliable liquid packaging machine supplier is critical for the smooth operation of any business involved in manufacturing. A supplier plays a pivotal role not only in providing machines but also in ensuring they meet the specific needs of your operations.
Evaluating Supplier Credentials
When choosing a supplier, it’s essential to consider their credentials. Reputable suppliers typically have certifications that affirm their adherence to industry standards. Look for suppliers who have been in the business for several years, as their experience often translates into a better understanding of various market needs and challenges. You can also assess their quality assurance protocols, which should reflect their commitment to providing high-quality equipment.
Comparing Product Offerings
Not all suppliers offer the same range of products. Some may specialize in specific types of liquid packaging machines, while others may provide a broader array of options. When comparing offerings, consider factors such as:
- Machine Types: Ensure they provide the specific type of machine that fits your production process, whether filling, capping, or labeling.
- Customization: Check whether they offer machines tailored to your product specifications or industry requirements.
- Brands and Models: Look for established brands known for reliability and performance.
Understanding Customer Support Services
The relationship with a supplier extends beyond the initial purchase. Strong customer support is integral, particularly when dealing with machinery that requires maintenance and troubleshooting. Consider the following:
- Technical Support: Ensure they provide comprehensive technical support, including installation guidance and machine troubleshooting.
- Training Services: Find out if they offer training for your staff to ensure optimal use of the machinery.
- Spare Parts Availability: Reliable suppliers should have readily available parts for maintenance and repair, minimizing downtime.
Key Features of Efficient Liquid Packaging Machines
To maintain a competitive edge and streamline production, it’s vital to invest in efficient liquid packaging machines. Here are some features to look for:
Automation and Speed Efficiency
Modern liquid packaging machinery should come equipped with automation features that enhance production rates without compromising quality. Automated systems can significantly reduce human error and increase output. When assessing machinery, inquire about the machine’s speed, how many containers it can fill per minute, and whether it can adjust to varying production volumes seamlessly.
Customizability and Adaptability
As product lines change, it is essential for machines to be adaptable. Machines that can accommodate different container sizes, volumes, and packaging materials help in maintaining flexibility in production. A good liquid packaging machine supplier should be able to provide equipment that can evolve with your production needs.
Maintenance and Durability
Investing in durable machinery is crucial to the long-term sustainability of your operations. Look for features that facilitate easy maintenance, such as removable parts for cleaning, access to sensors, and clear user manuals. The frequency and cost of maintenance should also be discussed upfront with the supplier to avoid unexpected expenses later on.
Common Challenges in Liquid Packaging and Solutions
Despite advancements in technology, various challenges can arise during the liquid packaging process. Addressing these challenges promptly can improve efficiency and product quality.
Dealing with Different Liquid Viscosities
Different liquids exhibit varying viscosities, which can affect how they flow through filling machines. Products like sauces and creams require specific machinery capable of handling thicker liquids. To overcome this challenge, it’s essential to choose filling machines that can adjust to different viscosities through programmable settings or specialized configurations.
Ensuring Package Integrity
Package integrity is vital for preventing leaks and contamination. Ensure your liquid packaging machines come equipped with proper sealing technologies, whether heat seals for pouches or screw caps for bottles. Regular audits of the filling process and package integrity tests can also help maintain quality standards.
Mitigating Contamination Risks
Contamination can occur at various stages of the packaging process, particularly in the food and pharmaceutical industries. Employing machines with integrated sterilization features and ensuring strict hygiene protocols are in place during the manufacturing process can mitigate these risks. Regular cleaning schedules and using machines constructed from non-reactive materials can also help maintain a contamination-free environment.
Future Trends in Liquid Packaging Solutions
The liquid packaging industry is experiencing rapid changes, driven by technology, consumer preferences, and environmental concerns. Staying updated with these trends can provide businesses with a strategic advantage.
Sustainability and Eco-Friendly Packaging
As the world becomes more environmentally conscious, businesses are shifting towards sustainable packaging solutions. This includes using recyclable materials and reducing waste through innovative packaging designs. Suppliers of liquid packaging machines are increasingly integrating eco-friendly solutions into their offerings, such as biodegradable materials that consider the lifecycle of the product.
Smart Technology Integration
The integration of IoT (Internet of Things) technology into liquid packaging is creating smarter production environments. Real-time data tracking can improve operational efficiency, enhance maintenance schedules, and optimize production processes. Smart machines can communicate with each other, allowing for automated adjustments and reducing the need for human intervention.
Evolving Consumer Preferences
Consumers today are more informed and concerned about the products they purchase. They prefer convenience, transparency in packaging, and eco-friendly options. Suppliers must adapt to these evolving preferences by offering advanced inline labeling, a range of packing options, and ensuring full traceability of their products. Staying attuned to these changes can position brands as leaders in a competitive market.