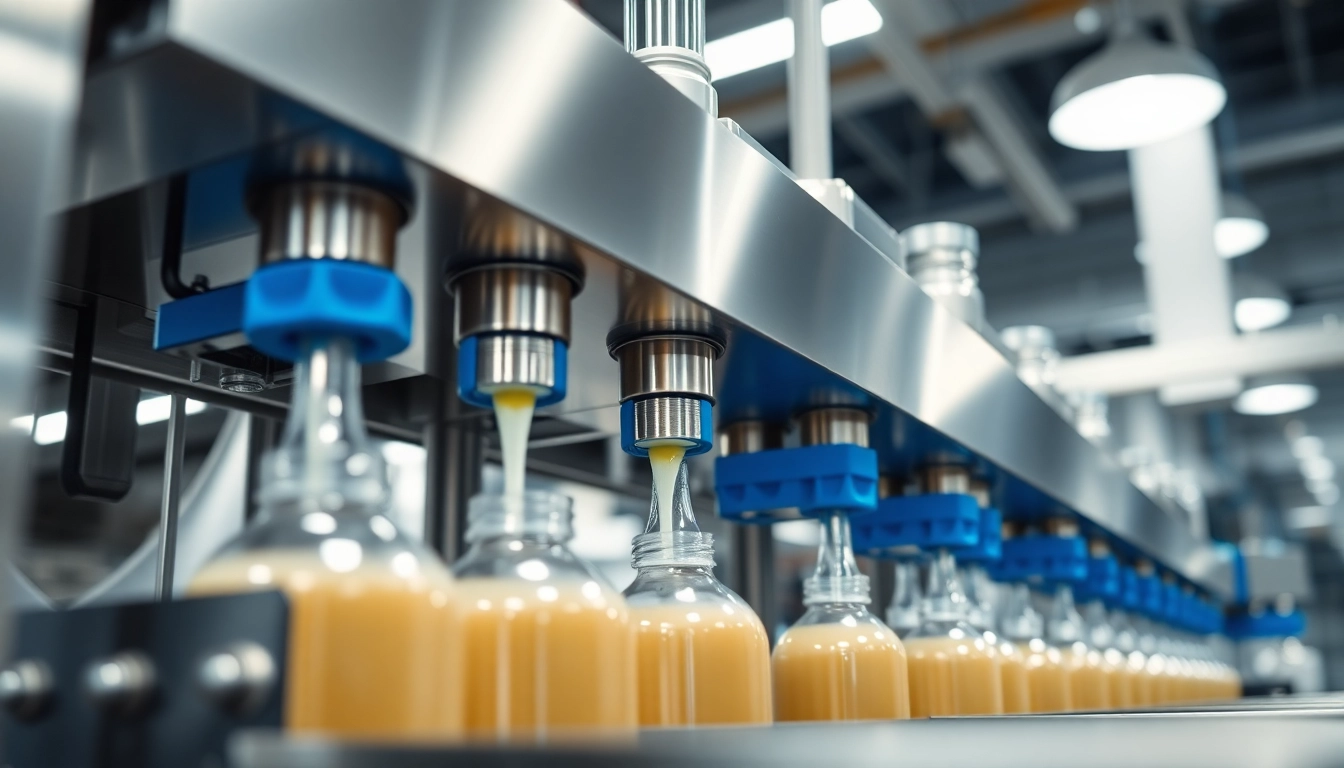
Understanding Liquid Packaging Machines
What Are Liquid Packaging Machines?
Liquid packaging machines are specialized industrial devices designed to package liquid products efficiently and accurately. These machines play a crucial role in various sectors, including food and beverage, pharmaceuticals, chemicals, and personal care. Their primary function is to fill containers—such as bottles, pouches, and cartons—with liquids ranging from water and juices to syrups and thick creams, ensuring that products remain safe and hygienically sealed throughout the supply chain.
Modern liquid packaging machines increasingly integrate advanced technologies, which enhances their efficiency, precision, and adaptability to different product types. They are vital for businesses looking to streamline their packaging processes and meet rising consumer demands for quality and speed. To explore comprehensive solutions in this area, you can refer to a reliable Liquid Packaging Machine Supplier that can meet your specific needs.
Types of Liquid Packaging Machines
Liquid packaging machines come in several varieties, each tailored to different types of liquids and packaging requirements. The main types are:
- Filling Machines: These machines are used for filling containers with liquids. They can be further categorized into volumetric, gravimetric, and piston filling machines, each suited for specific viscosity levels and container shapes.
- Sealing Machines: After filling, sealing machines securely close containers to prevent contamination. Various sealing methods include heat sealing, induction sealing, and screw capping.
- Labeling Machines: Essential for branding and information dissemination, these machines apply labels to the sealed containers, enhancing product visibility and compliance with regulatory requirements.
- Palletizing Machines: These systems automate the grouping and stacking of packaged products onto pallets for easier transportation and storage.
- Sachet Filling Machines: Focused on smaller quantities, these machines fill and seal pouches containing liquids like sauces, spices, and pharmaceuticals.
Benefits of Using Liquid Packaging Machines
The adoption of liquid packaging machines offers several advantages, making them an invaluable asset for production lines:
- Increased Efficiency: Automated processes minimize human error and speed up production times, allowing businesses to meet higher demand levels.
- Consistency and Quality: Advanced technologies ensure uniform filling, sealing, and labeling across batches, which is critical for maintaining product quality.
- Cost-Effectiveness: By reducing labor costs and waste, businesses benefit from lower operational expenses, enhancing profitability.
- Customization: Many machines can be adjusted to handle different liquid types and packaging formats, providing flexibility to respond to market changes.
- Compliance and Safety: Enhanced sealing techniques and hygienic designs help meet health and safety standards, protecting both the consumer and the product.
Choosing the Right Supplier
Key Factors to Consider
Selecting the right liquid packaging machine supplier is critical to the success of your packaging operations. Factors to consider include the supplier’s experience, range of products offered, and customer reviews. Additionally, assess the supplier’s ability to provide customized solutions and their responsiveness to your queries and service needs.
Assessing Supplier Reliability
Reliability is paramount in equipment suppliers. Check their track record through customer testimonials and case studies. A reputable supplier will have a portfolio showcasing successful implementations across various industries. Certifications and compliance with international standards (such as ISO) further bolster a supplier’s credibility.
Understanding Pricing Structures
Pricing can vary significantly based on the machine’s capabilities, features, and the supplier’s brand reputation. Be sure to obtain detailed quotes that break down initial costs, operating expenses, maintenance, and any additional fees related to service or support. Don’t overlook the long-term value of investing in quality machines that will last longer and deliver better results, even if they come with a higher upfront cost.
Technical Features of Liquid Packaging Machines
Automation and Efficiency
Today’s liquid packaging machines are heavily automated, resulting in increased efficiency. Many systems utilize advanced sensors and controls that monitor and adjust operations in real-time. This automation reduces downtime and enhances throughput, enabling businesses to scale their operations without compromising quality.
Additionally, advanced technologies such as Artificial Intelligence (AI) and the Internet of Things (IoT) allow machines to communicate with each other and provide valuable data analytics that can help optimize performance further.
Versatile Applications Across Industries
Liquid packaging machines find applications across many industries. For example:
- Food and Beverage: From small sachets of sauces to large containers of juices, packaging machines ensure that products remain fresh and consumable.
- Pharmaceuticals: Precise filling and sealing technologies are critical for ensuring dosages are accurate and products are contamination-free.
- Chemicals: Chemicals often require robust packaging solutions to handle corrosive substances safely.
- Cosmetics: Liquid packaging in this sector needs to be visually appealing and protect sensitive formulations.
Maintenance and Support Services
An often overlooked aspect when selecting a supplier is the maintenance and support services they provide. Regular maintenance is crucial for ensuring the longevity of packaging machines. Suppliers should offer technical support, training for operating the machinery, and access to spare parts. Long-term partnerships with suppliers who offer reliable support can improve uptime and productivity.
Common Challenges with Liquid Packaging
Addressing Common Issues
Despite the advantages of automated liquid packaging, several challenges can arise. Common issues include:
- Product Leakage: Poor sealing can lead to leaks, resulting in product loss and contamination. Regular checks on seal integrity can mitigate this issue.
- Inaccurate Fill Levels: Incorrect filling can lead to wasted product and income loss. Calibrating machines regularly and employing weight-based systems can help maintain accuracy.
- Changeover Times: Switching production to accommodate different products can lead to downtime. Choosing machines designed for quick changeovers can enhance flexibility.
Best Practices for Seamless Operations
Implementing best practices can help address the challenges of liquid packaging. Regular staff training, preventive maintenance schedules, and utilizing technology for real-time monitoring can significantly enhance operational efficiency. Also, fostering open communication between production and maintenance teams can help identify issues swiftly and reduce downtime.
Real-Life Case Studies
To illustrate how common challenges can be effectively managed, consider a beverage manufacturer that faced issues with inconsistent fill levels due to frequent line changeovers. By investing in versatile filling machines that allowed for quick adjustments and implementing a rigorous maintenance routine, the company improved its overall efficiency and reduced waste significantly.
The Future of Liquid Packaging Technology
Innovations on the Horizon
The liquid packaging sector is continually evolving, with innovations driven by sustainability and consumer preferences. Upcoming trends are likely to feature enhanced automation, machine learning applications for predictive maintenance, and smarter packing solutions that adapt to consumer demands swiftly.
Environmental Considerations in Packaging
As consumer awareness of environmental issues grows, packaging suppliers must innovate to reduce their ecological footprint. This includes developing machines that use less material, facilitating recycling processes, and utilizing more sustainable packaging materials. Companies that lead the way in environmentally friendly practices will likely gain a competitive edge in the marketplace.
Adapting to Market Changes
The liquid packaging industry must remain agile to adapt to changing market conditions, including fluctuations in consumer preferences, regulatory changes, and global supply chain challenges. Companies that can pivot quickly and invest in flexible solutions will thrive in an increasingly competitive landscape.