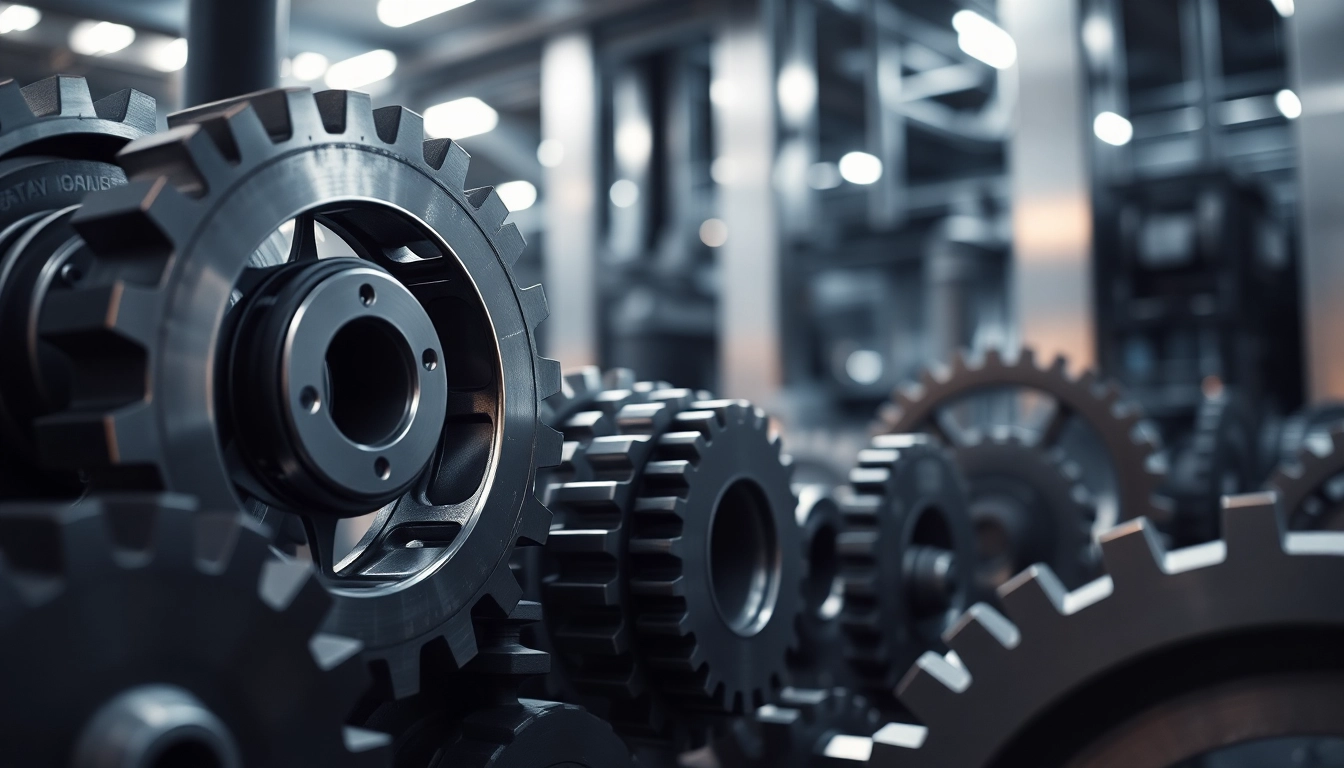
Understanding byd Gears: A Comprehensive Overview
What are byd Gears?
BYD gears are integral components used in a variety of machinery and systems, designed specifically to transmit power from one part to another through rotational motion. As critical elements in mechanical design, these gears ensure smooth operation across various applications, ranging from automotive to industrial sectors. The term “BYD” itself stands for “Build Your Dreams,” reflecting the company’s commitment to innovative technology and sustainable solutions.
BYD gears are known for their precision, durability, and reliability. They are engineered using high-quality materials and cutting-edge manufacturing processes that not only enhance their performance but also extend their lifespan. Whether it’s a simple gear for a small machine or a complex system involving multiple gear types, understanding the nuances of BYD gears is crucial for any engineering or commercial project.
Key Features of byd Gears
BYD gears boast several key features that make them highly sought after in various industries:
- High Precision: Manufactured to exact specifications, these gears exhibit minimal tolerances, ensuring that they fit seamlessly into their operational environments.
- Robust Material Selection: BYD uses advanced materials tailored for specific applications, enhancing both strength and resistance to wear and tear.
- Innovative Design: Modern design techniques, including computer-aided design (CAD) and simulation software, allow for the development of gears optimized for efficiency and power transmission.
- Customization: BYD gears can be customized to meet the unique requirements of various applications, ensuring optimal functionality in diverse scenarios.
- Eco-Friendliness: As part of BYD’s commitment to sustainability, many gears are manufactured using environmentally friendly processes, minimizing waste and promoting recycling.
Applications in Various Industries
BYD gears find applications in a multitude of sectors. Here are a few notable examples:
- Automotive: Used in transmissions, steering mechanisms, and other components, BYD gears contribute significantly to vehicle efficiency and performance.
- Renewable Energy: In wind turbines and solar trackers, these gears help optimize energy capture and distribution, playing a crucial role in sustainable energy solutions.
- Aerospace: High-precision gears are vital in aircraft systems, ensuring safe and efficient operation under extreme conditions.
- Industrial Machinery: From conveyors to heavy machinery, BYD gears are integral in enhancing productivity and operational reliability.
How to Choose the Right byd Gears for Your Needs
Assessing Project Requirements
Choosing the right BYD gears begins with a thorough assessment of project requirements. This includes understanding the specific application, the load characteristics, and the operating environment. Key considerations may include:
- Torque and Load Capacity: Determine the maximum load the gears must handle, which will influence size, material, and design.
- Speed Requirements: Evaluate the speed at which the gears will operate to ensure compatibility with other components in the system.
- Operating Environment: Consider factors like temperature, humidity, and potential exposure to corrosive materials, as these can affect gear longevity.
- Space Constraints: Measure available space for installation to determine the size and configuration of the gears.
Comparing Different Types of byd Gears
BYD offers an array of gear types, each with unique characteristics suited for different applications. Here are some common types:
- Spur Gears: Ideal for parallel shafts, offering simple design and efficient power transmission.
- Helical Gears: Known for smoother and quieter operation, they are perfect for high-speed applications.
- Bevel Gears: Used in applications requiring angular motion, such as in automotive differentials.
- Worm Gears: Useful for high reduction ratios and applications where space is limited.
When comparing gear types, consider the specific demands of your project and how each gear type meets those needs. Engaging with BYD representatives for technical insights can be very beneficial in this process.
Cost Considerations and Budgeting
Understanding costs associated with BYD gears is crucial in budgeting effectively for a project. Costs can vary based on materials, design complexity, and manufacturing processes. Here are some steps to consider when budgeting:
- Material Costs: The choice of materials affects not only cost but also performance and durability. High-performance materials may incur a higher upfront cost but can save money in the long term through reduced maintenance.
- Manufacturing Complexity: Custom designs or advanced manufacturing techniques can increase costs, so consider whether standard solutions would suffice for your needs.
- Supplier Relationships: Building a relationship with suppliers like BYD can lead to bulk purchase discounts or favorable terms.
- Life Cycle Costing: Evaluate not just the purchase price but the total cost of ownership, including installation, maintenance, and potential replacements.
Installation and Maintenance of byd Gears
Step-by-Step Installation Guide
Installing BYD gears requires careful attention to detail to ensure optimal performance. Here are step-by-step instructions for installation:
- Preparation: Gather all necessary tools, safety gear, and the specific BYD gear components.
- Clean the Installation Area: Ensure that the area where the gears will be installed is clean and free of debris.
- Verify Compatibility: Check that the gears are compatible with existing components in terms of size and specifications.
- Align the Gears: Proper alignment is critical to prevent premature wear. Use alignment tools, if necessary, to achieve accuracy.
- Secure the Gears: Use the appropriate fasteners to secure the gears in place, ensuring they are tightened to the manufacturer’s specifications.
- Conduct Tests: After installation, conduct a test run to ensure smooth operation and monitor for any unusual noises or behavior.
Best Practices for Gear Maintenance
To maximize the longevity and performance of BYD gears, implement a structured maintenance plan that includes:
- Regular Inspections: Schedule routine inspections to check for signs of wear, misalignment, or damage.
- Lubrication: Ensure proper lubrication as per manufacturer guidelines to minimize friction and wear.
- Cleaning: Keep gears and surrounding areas clean to prevent contamination that can affect gear function.
- Monitor Operating Conditions: Keep an eye on operating temperatures and loads to ensure they remain within specified ranges.
Common Issues and Troubleshooting
Despite rigorous maintenance, issues may still arise. Here are some common problems associated with gears and their possible solutions:
- Noisy Operation: Often a sign of misalignment or insufficient lubrication. Inspect and adjust alignment or apply additional lubricant.
- Excessive Wear: This could result from harsh operating conditions or poor lubrication. Review operating environments and maintenance practices.
- Gear Slippage: Check for gear compatibility and ensure that all fasteners are secure.
Maximizing Performance with byd Gears
Achieving Optimal Efficiency
To enhance the operational efficiency of BYD gears, consider the following strategies:
- Optimize Design: Engage in collaborative design processes to tailor gears to specific applications, improving efficiency ratios.
- Regular Performance Reviews: Analyze performance data regularly to identify improvement opportunities.
- Educate Users: Provide training on the proper use and handling of gears to minimize user-induced errors.
Performance Metrics and Tracking
Tracking the performance of BYD gears can be facilitated through the following metrics:
- Efficiency Ratio: Measure output power against input power to determine overall system efficiency.
- Wear Rate: Monitor wear against expected rates to determine if remediation is necessary.
- Operational Uptime: Track the percentage of time the system operates efficiently without failure.
Case Studies: Success Stories with byd Gears
Examining real-world applications provides insights into the effectiveness of BYD gears. A notable case involves a leading renewable energy firm that integrated BYD helical gears into its wind turbines. The new gearing system improved both efficiency and longevity, leading to a 20% increase in energy output while significantly reducing maintenance costs. Companies can draw valuable lessons from such case studies, tailoring their implementation strategies to replicate similar success.
The Future of byd Gears in Industrial Applications
Emerging Trends in Gear Technology
The field of gear technology is rapidly evolving. Innovations such as additive manufacturing and advanced materials are paving the way for more efficient and sustainable gear production. With the increasing adoption of IoT (Internet of Things), the future gears may feature embedded sensors for real-time monitoring, allowing for predictive maintenance and enhanced operational control.
Sustainability and Innovation in byd Gears
Sustainability remains at the forefront of BYD’s mission, and innovative practices are being implemented in the gear production process. From sourcing recyclable materials to developing energy-efficient manufacturing techniques, BYD is setting a benchmark for eco-friendly practices in the manufacturing sector.
Preparing for Future Developments
To remain competitive, companies should stay informed about advancements in gear technology and actively engage in training and development for their personnel. This proactive approach will help businesses leverage new technologies and methodologies to enhance operational efficiency.