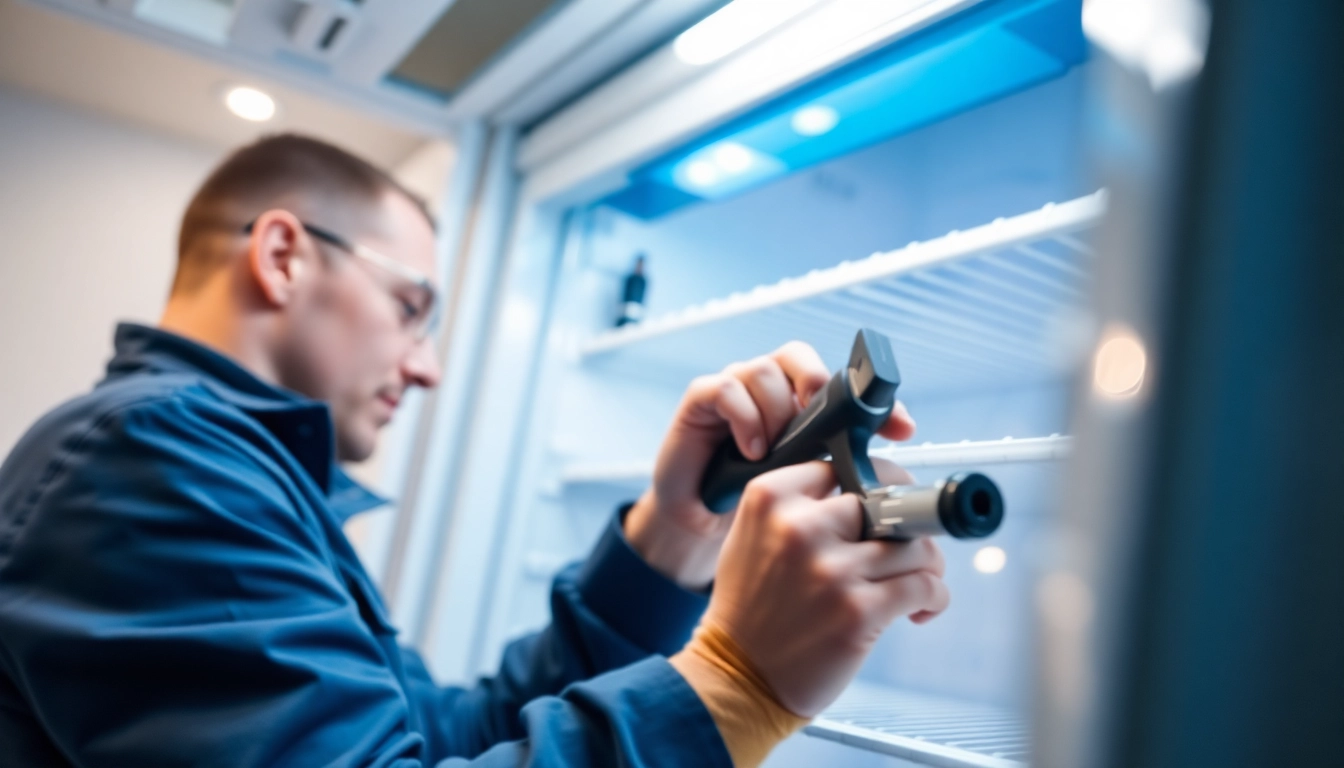
Understanding Walk in Freezer Repair Needs
As businesses increasingly rely on commercial refrigeration systems, understanding walk in freezer repair becomes essential for continuity and efficiency. Walk-in freezers are integral for storing perishable goods, and malfunctioning units can lead to significant losses. This article delves into the various aspects of walk-in freezer repair, including identification of repair needs, diagnosis of common issues, the repair process, preventive maintenance, and selecting the right repair service.
What is a Walk in Freezer?
A walk-in freezer is a large refrigerated space designed for storing significant quantities of perishable products, typically found in restaurants, supermarkets, and warehouses. These units maintain low temperatures, typically between -10°F to 0°F, to ensure the freshness of meats, dairy, and frozen goods. Unlike traditional freezers, walk-in models allow personnel to walk inside, facilitating easy access to large quantities of stock.
Common Signs Your Freezer Needs Repair
Recognizing the signs of freezer dysfunction is crucial for preventing product loss and escalating repair costs. Common indicators that your walk-in freezer may need repair include:
- Inadequate Cooling: If temperatures within the freezer exceed the set levels, it can lead to spoilage.
- Increased Energy Bills: A spike in energy costs may suggest that the unit is working harder than it should due to inefficiencies.
- Unusual Sounds: Uncommon noises like hissing, clicking, or grinding may indicate mechanical issues.
- Icing or Frost Buildup: Excessive frost accumulation can hinder the freezer’s performance and requires prompt attention.
- Moisture Inside the Freezer: If you notice water pooling or excessive condensation, it could suggest a refrigerant leak or other malfunction.
Why Timely Repairs Matter
Delaying repairs can result in more severe issues, escalating repair costs, and potential loss of refrigerated inventory. It’s essential to address problems as soon as they arise to maintain operational efficiency, safeguard products, and reduce downtime. Regular monitoring and proactive maintenance can also prolong the lifespan of your walk-in freezer.
Diagnosing Walk in Freezer Issues
Identifying Common Problems
Understanding the most common problems associated with walk-in freezers is key to diagnosing issues effectively. Below are some prevalent issues:
- Compressor Failures: The compressor is critical for regulating temperature. Failure can lead to a malfunctioning unit that doesn’t maintain proper levels.
- Defrost System Problems: Issues with the defrost heater can lead to ice accumulation, making it difficult for the freezer to operate correctly.
- Thermostat Malfunctions: A faulty thermostat can lead to inaccurate temperature readings, resulting in improper food storage conditions.
- Refrigerant Leaks: Leaks can significantly affect the efficiency and performance of the freezer.
Tools Needed for Diagnosis
Effective diagnosis of walk-in freezer issues requires specific tools, including:
- Thermometers: For checking the temperature inside the freezer accurately.
- Multimeter: Helps check electrical components, ensuring that systems are properly functioning.
- Manifold Gauge Set: Useful for checking refrigerant levels and diagnosing compressor issues.
- Insulation Tester: To evaluate electrical insulation for potential leaks.
When to Call a Professional
While some minor issues can be resolved via DIY efforts, more serious problems necessitate professional intervention. Signs that you should call a technician include:
- If the temperature shows no improvement despite your efforts to adjust settings or clean components.
- If you encounter strange sounds coming from the unit, indicating possible mechanical failure.
- Persistent frost or icing issues despite attempts to resolve them.
- If you suspect a refrigerant leak, which can be hazardous if not managed properly.
The Walk in Freezer Repair Process
Initial Assessment and Costs
The repair process begins with an assessment to determine the underlying issues. A qualified technician will evaluate the unit’s components, including the compressor, evaporator coil, and defrost systems. The costs associated with repair can vary widely based on the issue, the parts needed, and the labor involved, ranging anywhere from $250 for minor issues to over $1,000 for comprehensive repairs. Getting quotes from multiple service providers can help you make an informed decision.
Repair Techniques and Solutions
Once the problem is diagnosed, various repair techniques can be implemented:
- Compressor Replacement: If the compressor is deemed faulty, replacing it is crucial for restoring freezer functionality.
- Refrigerant Charge: If low refrigerant levels are indicated, recharging the system is often necessary.
- Defrost Heater Repair: If ice accumulation is an issue, repairing or replacing the defrost heater can restore proper function.
- Thermostat Replacement: Installing a new thermostat can correct temperature inaccuracies and improve efficiency.
Maintaining Efficiency Post-Repair
After repairs, maintaining your walk-in freezer is vital to ensure durability and efficiency. Following the repair process, encourage practices such as:
- Regular inspections to catch issues early.
- Conducting temperature checks regularly to ensure proper operation.
- Keeping the unit clean and free of dust to optimize airflow and efficiency.
Preventive Maintenance Tips for Walk in Freezers
Regular Cleaning and Upkeep
Scheduled cleaning is crucial for walk-in freezers. Ensure that the coils are cleaned from dust and debris, as this can hinder temperature regulation. Additionally, inspection and cleaning of door seals are important to prevent air leaks, which can drastically increase energy consumption.
Monitoring Temperature and Performance
Establish a routine for monitoring temperature levels and performance metrics. Using data loggers can assist in tracking performance over time, as fluctuations in temperature could signal an impending issue before it becomes catastrophic. Keeping a detailed log can also aid technicians in diagnosing issues during maintenance checks.
Scheduling Professional Inspections
Regularly scheduled inspections by professional technicians can potentially save hundreds of dollars in emergency repair costs. These inspections should include checks of the electrical systems, refrigerant levels, and mechanical components to identify potential problems before they escalate.
Selecting a Reliable Walk in Freezer Repair Service
What to Look for in a Repair Technician
When choosing a repair technician, consider their expertise and experience with walk-in freezer systems specifically. Look for credentials and certifications that demonstrate their capabilities and understanding of refrigeration systems. An ideal technician should also exhibit strong problem-solving skills and have access to the tools required for effective diagnosis and repair.
Reading Reviews and Gaining References
Research potential repair services by reading online reviews and seeking recommendations from industry contacts. Customer feedback can provide valuable insight into the technician’s reliability and quality of work. Consider asking for references from past clients to gauge their satisfaction with the services provided.
Comparing Costs and Services Offered
Before finalizing a repair service, obtain quotes from several companies. Analyze what each quote includes regarding services, warranties, and potential follow-up visits. Remember that the cheapest option may not always be the best; focus on the value of the service provided rather than solely on cost.